We will become masters, not slaves of automation
18 September 2017
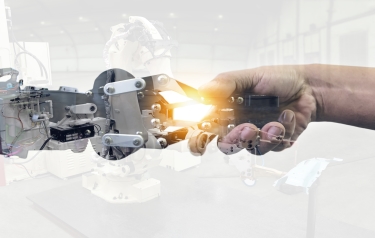
Shutterstock image
It is almost impossible to avoid the debate on man vs machine whenever the subject of automation is brought up. People hear the word ‘robot’ and immediately think we’re on the brink of some Terminator-style apocalypse. While this isn’t the case, at least not in this lifetime, there is still a very serious concern that the UK’s adoption of robotics (automation) will lead to job displacement.
Connectivity spoke to Graeme Philp, CEO of GAMBICA, who’s been leading the working group on automation and jobs as part of the UK’s Industrial Digitalisation Review (IDR). He discounts the more lurid scare stories about robots taking over the world and strongly argues that automation will allow us to become masters of technology.
Let’s start by taking a look at the UK car industry. The UK didn’t automate seriously in the 60s and 70s, while others were, and it was only one or two foreign companies buying the remains of the industry that then forced the automation. Right now, we have a thriving industry that employs a significant number of people.
| Vehicles produced | People employed | Productivity – vehicles per person |
1984 | 1.1 million | 298,000 | 3,700 |
2011 | 1.3 million | 124,000 | 10,500 |
2016 | 1.8 million | 151,000 | 11,900 |
Yes, as this table illustrates, the car industry does employ less people than it did in its hay day, 151,000, which is roughly half compared to 1984, but how many would we have employed if we hadn’t automated? Arguably, we wouldn’t have had an industry at all.
The mistake people make is they believe we can freeze industry as it currently is but if we do that, other countries won’t and exactly what began to happen to our car industry will happen to our general industry; we will risk being left behind. There is no ‘let’s stay as we are’ option.
As has been the case with industrial revolutions and automation in the past, there is an element of job displacement and job creation. Industry believes that the job creation will exceed the job displacement, although the displacement is likely to come early and the creation will take longer.
Displacement vs creation
Most jobs nowadays require human added value in one form or another, which involves us using our intuitive skills, our judgement and all the other attributes that make us sentient beings rather than just programmed machines. Unlike robots, we don’t run on algorithms, we are somewhat more sophisticated.
Arguably one benefit that the UK has in facing this technological revolution is that it largely offshored manual, repetitive, low added value manufacturing tasks a while ago meaning it’s very rare to find jobs that are wholly manual and repetitive which means that it’s difficult for automation to completely replace a job. What automation can do is perform some tasks quicker, more efficiently and more safely than a human.
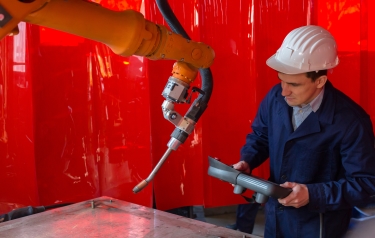
Shutterstock image
But for those jobs that are displaced by new technology, it is believed that a greater number of jobs will be created. The evolution of technology is one way this will be achieved. If we are going to have truly connected industries, we are going to need people to design, implement and maintain them. It also means we will become more efficient and there should be an economic growth associated with that. Therefore, jobs in IT, R&D and data analysis will naturally emerge.
This means a cultural shift is upon us; people are going to need to begin reinventing themselves, perhaps several times throughout their career. For the people that are likely to be displaced, they will be in mid-career and will find it harder to adjust. So we need to make it easier. Graeme’s view: there are very few jobs where an employee hasn’t added value by their human attributes. These people are trainable to take on higher paid jobs making the technology work for their companies. Employers need to create a mind-set where its employees don’t feel like they’re being replaced by technology but instead, becoming masters of it.
An example of this comes from one of Graeme’s previous employees, MTL Instruments. It actually increased the number of employees when it automated its factory. The people who were displaced were at the centre of the company’s plans, retrained and became machine programmers, production engineers etc. Ultimately several of these people formed the nucleus of the team which introduced lean manufacturing concepts to the company. Several of them have gone on to have entirely new careers as manufacturing consultants, helping other companies. Automation did not cause redundancy, in fact most people ended up in higher paid jobs. A great example of what is possible with the right mind-set, says Graeme.
I don’t want this to be thought of as naïve, wishful thinking, he continues, but the UK has a serious skills gap at the moment. You talk to any company about filling their engineering job vacancies, and if you’re not a household name like Rolls-Royce, Jaguar Land Rover or British Aerospace then it’s really difficult. These displaced people know a lot about your products and your production processes. It is possible with modest retraining to put this knowledge back to work for you. It’s all about involving the employees in the change process and giving them the confidence to step up.
The growing skills gap
We also need to get our younger generation trained up to an even greater extent than we are now, otherwise the gap will never close. The problem is, schools are not aligned with industry’s need and some even question whether it’s their responsibility. The most important thing we can teach children is the ability to learn. This will give them the talent to pick up on future skills that we aren’t yet prepared for.
In the past, we’ve always managed to create more jobs and there hasn’t been an industrial revolution (yet) where people have seriously said we need to backtrack. Whilst the past isn’t great at predicting the future, there is a lot of evidence that suggests change is always feared but seldom delivers the apocalyptic results predicted.
Brexit
Is Brexit going to affect this? It’s hard to argue that it won’t but Graeme suspects it won’t be as bad as we think. The Government’s “Great Repeal Bill” will ensure that existing EU legislation will be copied across into UK law and many in industry will be fighting to make sure we don’t then diversify from European standards and legislation, ensuring a smooth transition and some degree of certainty about the future.
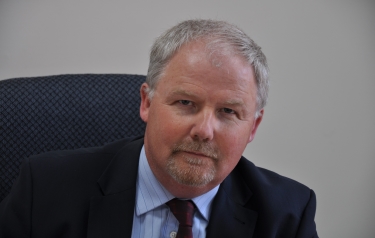
Graeme Philp is Chief Executive at GAMBICA
Where Brexit may have a bigger impact will be in the appetite for investment. For smaller companies especially; if they’re going to make a significant investment in automation they need to feel the financial environment is stable and current uncertainty over Brexit means that this isn’t the case.
The Government and industry therefore need to educate businesses, making sure everyone is armed with all the information necessary to make the right decisions and encouraged to embrace this new era of digitalisation. This is where the Industrial Digitalisation Review (IDR) comes in.
The Industrial Digitalisation Review (IDR)
A group of businessmen and academics from across the UK have come together to lead a review for the Government around industrial digitalisation. The team, which is led by Juergen Maier, CEO of Siemens UK, Phil Smith, Chairman of Cisco UK and Dave Stokes, CEO, IBM UK & Ireland, will advise on the impacts of digitalisation across UK manufacturing and industrial sectors, and how government working in partnership with industry can maximise the opportunities from driving digitalisation and automation.
The recommendations from the review should ensure that industrial digitalisation provides a significant boost and opportunity for British industry rather than a downside, especially on UK jobs.
You can read the interim report here - this does not represent the final recommendations to be issued to the Government this Autumn.
Graeme Philp is Chief Executive at GAMBICA, the Trade Association for Instrumentation, Control, Automation and Laboratory Technology in the UK. The Association’s primary objectives are to further the successful development of the industry and to promote the competitiveness and profitability of member companies.
Contact Details and Archive...