Using the world's fastest robot to achieve speedy ROI for UK produce retailer
11 October 2017
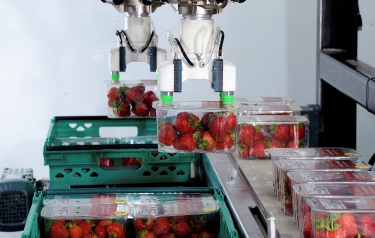
The unique four arm Delta has a greater reach and dexterity
When case loading OEM specialist Brillopak was approached by a leading UK retailer to improve punnet throughput, they used the latest Omron technology to help them take a fresh approach to punnet loading.
Punnets are widely used in the food industry for the packaging of fresh fruit and meat. Not only are they attractive and clearly display the size and quality of the produce, they also maintain product integrity to minimise waste. But while punnets perform well on the shelves, they can cause issues for manufacturers at the back-end of the production line.
Lines that handle punnets are usually highly automated, and as automation becomes faster and more efficient, the throughput increases accordingly. However, this higher throughput places a strain on the end of line packing function, which has to place the punnets into crates and cases at the same speed as the line. Traditionally, this process is achieved by packing in layers: the exact number of punnets to make a layer is accumulated at the end of the line and placed in the box as a full layer. But if one punnet is dropped or falls off the line, the line is interrupted. Faster lines exacerbate this problem and lead to even more stoppages, negating any benefits from the higher throughput of new machines.
The layer pack concept also relies on the punnets being laid out in a uniform way, but the current trend towards providing a wider variety of product offerings and sizes makes this a challenge. Another drawback is that even though the end of the line is automated, there is still a need for manual labour. However, it is becoming harder to recruit front-line staff and Brexit is set to make this situation even worse. And even when workers are available, the rising minimum wage brings additional expense.
These were the issues facing a leading UK retailer when it decided to upgrade its production line. The company turned to Brillopak to provide the new line, which would include a solution to the punnet packing problem. Specialising in solutions for fresh produce since 2010, Brillopak designs and manufactures premium quality, small footprint, robotic packing and palletising machines. One way that Brillopak differentiates itself from rivals, is by designing and manufacturing robot heads in-house for custom applications that require specialised handling.
After considering the project’s specification, Brillopak decided that the best way to accomplish the task was to single pick if possible. If the punnets could be individually packed, then it would solve both the problem with accumulation (meaning fewer stoppages) and require less staff. The retailer would also be able to pack the produce in a variety of ways, instead of a single direction.
To accomplish a single pick implementation at such a high rate would require a delta-type robot. Brillopak selected Omron’s Quattro Delta robot – the world’s fastest robot with a top speed pick rate of 300 per minute. For the last three years, Brillopak has exclusively used Omron technology for its automation systems, primarily because of Omron’s focus on the integration of its products. It means the communications, safety, control and other functions fall under one software solution, making programming easier and less time consuming.
Another first for Omron’s Quattro Delta is its unique fourth arm design, which allows it to reach 30 percent further than similar sized robots. The additional axis also allows the robot to tilt the load, making it much more flexible – ideal for placing packs in tight spaces, such as punnet crates.
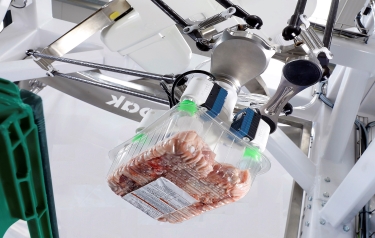
With 300 ppm, the Quattro is the world’s fastest robot
Brillopak designed and manufactured a bespoke line named Meteor, which incorporated two Quattro robots, one placed after the other and using Brillopak’s own custom heads. The heads use multiple vacuum cups, which each have their own generator, to provide a secure grip on the punnet. This is particularly useful when handling a punnet with multiple holes in the film lid, as it means that a single cup won’t break the vacuum seal for the rest.
To further protect the line from any downtime, Brillopak used Omron’s Pack Expert to set up packing formations to accommodate new products. The software can be used offline, has a drag-and-drop feature for better control of the packing process, and offers 3D simulation to provide a greater level of visibility. Once the retailer is happy with the new layout, it can be downloaded quickly to the line, keeping any stoppage to an absolute minimum.
Brillopak integrated the packing solution under the control of an Omron NJ PLC and Sysmac software, accessed by Omron HMIs. Intelligent design of the software and GUI for the HMIs was also essential to cutting downtime. Furthermore, as the line operator may not have English as a first language, the software for the HMI was specially designed to show the most likely actions in an intuitive way. Over time, Brillopak has shown that this approach is very effective in getting the line back up and running promptly, and requires less call-outs for engineers. The system also has a remote access feature, allowing Brillopak to access almost every part of the system to determine the cause of any stoppage. And as there was still additional performance available from the robots after matching the speed of the line, the solution is futureproof should the line ever be upgraded.
David Jahn, Managing Director of Brillopak, explains why such focus was placed on minimising downtime for the line: “For this installation, the customer demanded a return on investment in under two years. To achieve such a demanding target means keeping the line operating almost continuously. The line was specifically designed to eliminate the stops that occur frequently because of problems with accumulation and also to minimise the time taken to get the line up and running after changeovers, or any other stoppages, which can lead to over an hour of downtime every day.”
Omron Field Sales Manager, Andrew Shelley added: “Brillopak is a pioneer in the industry, and the company always stretches our latest technology to its limits through its innovation, such as in this example. This line installation is a perfect showcase of the capabilities of the new Omron Quattro Delta robot for packing applications, as well as the advantages that can be gained from the seamless integration of Omron products that are controlled through the dedicated Sysmac software.”
The completion of the Meteor line has shown that Brillopak’s decision to use an automated single pick solution to overcome the drawbacks found in the layer picking process was insightful and justified. The solution demonstrates that cutting downtime and staffing costs while improving efficiency is possible for punnet packing. The customer is now able to quickly perform changeovers to provide the wide variety of offerings that today’s consumers demand.
Contact Details and Archive...