Ocado’s I4.0 solutions make packing groceries that much smarter
Author : Paige West - Editor DPA & Connectivity
22 November 2017
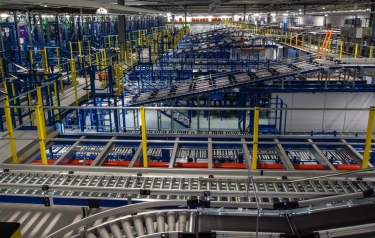
Ocado Dordon warehouse
The Connectivity Editor paid a visit to Ocado’s state-of-the-art warehouse at Hatfield in the UK to see how it combines robotics, machine learning, wireless communication, IoT, Cloud and big data technologies to function efficiently.
Ocado Customer Fulfilment Centres (CFCs) are its most established major distribution depots. Ocado started pilot deliveries from the Hatfield CFC1 in 2001, and today it completes around 150,000 orders per week. The warehouse is equivalent to 11 football pitches in size and stands 20 metres tall.
A combination of automation and people
It operates based on the popularity of items. For items that sell very quickly, pick aisles are used. The aisles are about 100m long and feature 10 work stations. Behind every pick aisle, there’s an automated crane that replenishes products based on an Ocado designed algorithm, which uses artificial intelligence to calculate what items are needed and where. Nothing is random, the algorithm learns from a number of factors, including seasonality - meaning the aisles can look very different in summer compared to winter.
A different system is used for items that are less popular. The system is essentially a goods to person system; instead of a personal shopper walking up and down a pick aisle, the goods come to them and the picking is done on the spot. This means less time walking and more spent picking.
The software not only optimally places products, it also optimally makes use of the workforce. For example, as orders pile up and certain areas become busy, the software will know more people are needed and the workforce can be moved appropriately.
Monitoring and management
Enter the control room, where Ocado’s engineering operations team oversees everything in the warehouse. This is done using systems designed to specifically help them. Two particular systems, built in-house, monitor every single piece of automation down to the individual part, so if anything goes wrong the team know which part needs fixing/replacing.
Another really important system displays just the conveyors and crates moving in the building. Barcodes are used to keep track of every order around the warehouse, clicking an individual crate will display the barcode and tell the operator what’s inside at any given time. Operators can also see if there’s any blockage on the conveyors and identify where it’s happening, using the system to figure out what went wrong.
The system is not only a monitoring tool but one for future improvements and changes; more conveyors can be added using simulation tools, allowing operators to predict what the flow would look like.
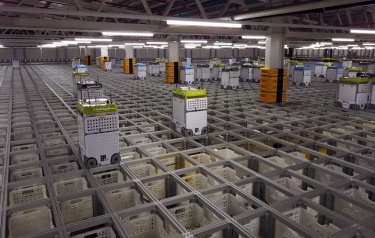
Ocado Andover CFC
History of engineering at Ocado
Taking a closer look at a system bought by Ocado from a third party supplier, it seems parts of the systems were originally designed for general merchandise retail, not grocery. Since grocery retail tends to move much faster than general merchandise, with Ocado needing to pick about 1.5 million items per day on average, Ocado had to re-write the software with this need in mind.
After re-writing the software, Ocado design engineers recognised more potential improvements to make the whole system even faster and efficient. As a result, Ocado become more involved in the hardware design and layout, recognising that they knew better than anyone the kind of changes that were needed.
Ocado needs to store more than 50,000 different items and one of the limitations on the system mentioned above, is the amount of items you can store. At the time of purchase, Ocado’s range was smaller so it was suitable but as the range started to grow, storage became a problem. So, the first improvement was to make the system bigger so it could store a bigger range of products. Other improvements were made to the pick stations; instead of having multiple storage boxes at the top and several customer orders at the bottom, it became one to one. Personal shoppers now only pick from one and pack from one, making the system faster and less confusing.
These improvements alone have made the system 40-50 percent faster meaning personal shoppers can pick 40-50 percent more items per hour.
Baggage system
In the early stages of the company, Ocado’s bagging process was done manually. Yet, it quickly because apparent this was an inefficient use of employees time and a rather boring activity. Ocado identified this problem and came up with a solution in-house; it designed a machine to automate the task. The new machine can complete approximately 800-900 bags an hour. Not only did Ocado design the machine but the plastic bags too, making them fully recyclable. As part of its Bag Recycle Bonus Scheme, Ocado customers can receive 5p for each carrier bag they recycle – both own-brand and other retailers.
Ocado Smart Platform
After the tour, Connectivity had the chance to speak with Ocado Engineering’s Design Manager, Vipin Pillai about the Ocado Smart Platform (OSP). This is a modular and scalable software and hardware platform designed to put the world’s largest retailers online.
The OSP Customer Fulfilment Centres (CFCs) include a robot grid that represents a breakthrough in engineering. The first OSP CFC went live in December 2016 and is located in Andover (CFC3), featuring 1,000 robots working together on two grids roughly the size of a football pitch each.
The grid is extremely dense and parallel; robots move on top of the grid which contains storage boxes filled with products. You can think of it as one giant goods to person system but instead of the system being split around a warehouse, everything is concentrated in one location. This creates a much more efficient use of space and an increase in speed. For example, to process an order of around 50 items in the Hatfield warehouse, it would take about 2-3 hours. This new system can complete an equivalent order in about 15 minutes.
The robots are completing two tasks; retrieving items to carry to pick stations and replenishing stock. The system is also designed for resiliency: if one of the robots happens to fail or runs out of battery, another one will automatically take over.
Individual robot battery life varies depending on the area in which they operate. Ocado has optimised its charging system in such a way that the battery life was extended as much as possible. The frequency at which the robot moves onto the chargers, how it leaves and how it performs is all monitored and analysed. Ocado is in the process of updating its battery technology and is therefore conducting a lot of research in this area.
An important point to note is that these systems are not designed to replace people but help them. There will still be people surrounding the system, replenishing stock, picking and packing and conducting engineering operations. It’s more about automation and the workforce working together.
The second OSP CFC (Erith CFC4) is currently under construction and is projected to be three times the size of Andover CFC3. When opened, it will be the largest automated warehouse for online grocery in the world.
About Ocado Engineering:
Ocado is the world’s largest online-only, delivery based grocery retailer. Its objective is to provide customers with the best shopping experience for service, range and price. To achieve this, it built a number of Customer Fulfilment Centres (CFCs): highly automated warehouses incorporating the latest automation, robotics and control systems. Building the CFCs and the automated systems powering them and overseeing their efficient operation is Ocado Engineering and Logistics Development – a skilled team of engineers specialised in mechanical, electronic, design for manufacture, safety, civil, controls or automotive engineering.
Contact Details and Archive...