PROFINET – the backbone for Industry 4.0
Author : Karsten Schneider, PI Chairman
01 February 2018
Industrial Communication is yet again in the position to change production automation. In Industry 4.0 the job at hand is to enable new business models by connecting the shop floor to IT systems. Karsten Schneider, PROFIBUS & PROFINET International (PI) Chairman talks us through the two fundamental requirements to make this work – connectivity and data.
In the past decades, field bus systems like PROFIBUS helped to enable modularisation in plants by allowing machine builders to develop pretested equipment which could be simply connected to a production line by a single field bus cable. Now in Industry 4.0 the job at hand is to enable new business models by connecting the shop floor to IT systems. Autonomous machines that can self-optimise production or machine learning algorithms which offer predictive maintenance are only two examples for Industry 4.0.
In PI we see two fundamental requirements to make this work – connectivity and data. Data is obvious. No data, no decisions – ergo no optimisation, predictions, analysis and the like. Data is often referred to as the new gold or oil. It drives these new business models. Data allows learning from the past and making assumptions of the future. But it is rarely mentioned, that only semantically qualified data is valuable. IT systems need to understand the data and its meaning to generate value from it. If engineers need to configure every single data point, profitability could hardly be achieved. Data must be available and self-explanatory for machines!
It is PROFINET & PROFIBUS Internationals (PI) role since almost three decades now to provide information models for plain raw data from the factory floor, so called Profiles. The PA profile for example standardises how process instruments are integrated into automation systems. The way how a temperature sensor transmits its data to the DCS is given across all vendors. There is no need to tell the DCS application, that the 3rd byte in the transmission is a temperature value measured in degrees Celsius. This is automatically setup by the configuration. Simplified engineering is the result. And of course there are many profiles for different industries today like safety, drives, energy management, asset management, etc. These profiles are defined by users and vendors in a neutral, open and standardised way. Profiles allow any system to understand the meaning of data and generate information from it.
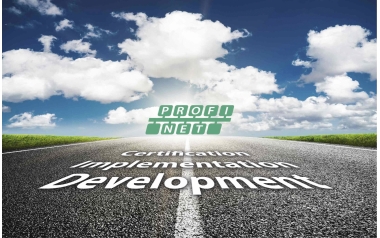
The second aspect is connectivity. Data is only valuable if you can access it. With PROFINET we lay the foundation by using standard Ethernet. This way not only PROFINET can be run on the cable, but any other Ethernet protocol can do so as well. This allows us to bring in OPC UA for vertical communication. OPC UA was made for the integration into IT systems. It has powerful mechanisms to structure data and define information models. This is why PI established a cooperation with OPC Foundation and setup a joint working group to define a mapping of PROFINET profiles to OPC UA – again to reduce the efforts for automation engineers. The first step is to standardise a companion specification for OPC UA for diagnostics and asset management. But vertical communication is just one use case. PI sees OPC UA as a perfect match for controller-controller communication. This way, cross vendors interoperability will be achieved among the different PLC systems. To go one step further, PI started to bring PROFIsafe, the profile for failsafe communication, to OPC UA as well. With this activity PI breaks new grounds and demonstrates its belief, that only cooperation between different organisations can solve the tasks of Industry 4.0. PROFINET and OPC UA nicely complement each other and integrate seamlessly.
To bring connectivity to a new level, PI is now going to adopt Time Sensitive Networking (TSN) for PROFINET to support converged IT and OT networks and make it even easier to send the data from the shop floor to IT systems or the cloud. TSN is a set of new IEEE standards that offer deterministic behaviour as known from the industrial Ethernet systems to the open IT networks. Furthermore this will bring higher bandwidth through GBit networks to PROFINET. Industry 4.0 applications rely on the transmission of data. It can be expected, that the traffic on industrial networks will magnify dramatically. For industrial communication systems to survive the next era of automation it will be essential to participate on the progress of IT networks. TSN is the technology that allows the use of standard IT Ethernet Controllers. Doing so, there is no need for dedicated, proprietary ASICs anymore to build automation equipment – a tremendous advantage for device manufacturers and users alike.
These are only some examples how PI shapes up PROFINET for future applications. PI has a history in going down new paths to sustain the technology for the upcoming decades. The adoption of TSN will make PROFINET fit for the future and by defining information models together with OPC Foundation, PI brings its knowledge to the standardisation community of Industry 4.0. This makes PROFINET the perfect backbone for Industry 4.0 applications.
Contact Details and Archive...