Realising the IIoT: Harsh environments demand rugged edge nodes
Author : Leah Langston, product marketing engineer, DAQ & Control, NI
30 April 2018
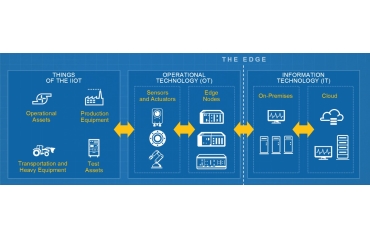
By 2019, at least 40 percent of IoT-created data will be stored, processed, analysed, and acted on at the edge
Though business leaders are eager to capitalise on the Industrial Internet of Things (IIoT), it’s difficult to fathom that 50 billion devices will be connected by 2020. For those in industry, it’s tempting to discount this number because it includes consumer technology such as smart phones and fitness trackers. However, it’s estimated that the industrial sector will account for nearly half of these new connected devices deployed between 2015 and 2025.
This means that engineers and scientists are in the driver’s seat for implementing the IIoT across factories, test laboratories, power grids, refineries, and infrastructure. Global processing industries are some of the earliest adopters of the IIoT, and it’s easy to see why. Unscheduled downtime of assets costs $20 billion annually, 80 percent of which is preventable.
However, it’s not just the global processing industries who see obvious benefits from the IIoT. Among business leaders, 95 percent expect their companies to use the IIoT within the next 36 months, and 87 percent believe it will contribute to long-term job growth.
Realising the Value of the IIoT
When it comes to the IIoT, we can expect to gain three key benefits:
• Increased uptime with predictive maintenance
• Boosted performance with control at the edge
• Improved product design and manufacturing through connected, real-world data
The first benefit that springs to mind the quickest is increased uptime with predictive maintenance. Today, the uptime of the most critical assets often rests on manual inspection by a few subject matter experts. Unfortunately, these experts are becoming harder to come by, and manual monitoring is not scalable across an entire fleet of assets. It’s estimated that only five percent of the data collected today is analysed. The IIoT has helped shine a light on what’s possible for using analytics and machine learning to predict the amount of serviceable life left on the asset and schedule the maintenance before a costly failure.
The second benefit involves increased and optimised performance. Smart machines deployed on production lines or in the field must be able to adjust parameters, such as temperatures or throughput, depending on information they receive from other machines up stream. The most ideal way to boost performance for these systems involves full autonomy on the part of the machine or asset. In this case, if machines can learn, either from other machines or through their own experiences, they can then tune control parameters and better adapt to their surroundings.
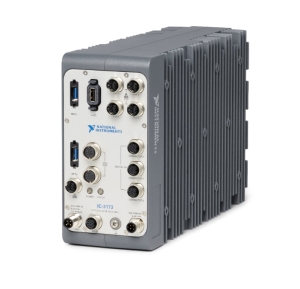
The IC-3173 (IP67) is the first Industrial Controller that is dust- and water-resistant, making it ideal for high-performance computing in spray-down and dirty environments
The final benefit of the IIoT is to improve the design and production of products. This is sometimes referred to as IoT for R&D. In this case, real-world data, such as usage data, is fed back into engineering to improve the next product generation. However, it’s about not only acquiring the data but also effectively managing it so that you can gain the valuable insights. Take, for example, Jaguar Land Rover. The company has hundreds of engineers who collectively generate 500GB of time-series data per day. With their previous solution, they analysed only 10 percent of their data. After implementing an IIoT solution, they increased that coverage to 95 percent, allowing them to address more design issues in the same amount of time.
These outcomes depend on several core technologies, but a key commonality is the need for intelligence at the edge. For example, the ability to process massive amounts of sensor data in real time is essential for implementing the sophisticated control for autonomous machines. But it’s not just limited to autonomous machines. It’s estimated that at least 40 percent of all IoT-created data will be stored, processed, analysed, and acted on at the edge. Practically, this makes a lot of sense. Implementing fleet-wide IIoT systems is much easier if your edge nodes communicate single “serviceable life” values instead of streaming raw vibration data back to a centralised data center. To maximise performance and reduce unnecessary data transfers, you must push decision-making down to edge nodes deployed at or near the “things.”
However, for edge nodes to perform the local analysis and control, they must meet specific requirements. These edge nodes must be rugged enough to be placed close to the sensors, while still maintaining the processing power for doing in-line analysis and control for massive amounts of data. In addition, they must be able to synchronise across the entire system, as well as integrate seamlessly into existing infrastructure.
Yet, another trend that has been growing alongside an increase in the overall number of sensors is the use of cameras. The global machine vision market is expected to reach $14.72 billion by 2022, growing at a CAGR of 8.9 percent from 2015 to 2022. This is not surprising, because vision provides a new level of insight into production and machinery that other sensors can’t. For example, we’ve all witnessed the mass incorporation of cameras in automobiles that support advanced driver-assistance features like blind spot monitoring or collision avoidance. These embedded cameras increase the insight that vehicles can gather about the world around them.
In the same way, adding more cameras to inspection systems and smart machines gives you increased insight about the quality of products or the health and productivity of machines. And though manufacturing engineers would like to implement more quality inspection tasks on their production lines, they are limited by the ability to do in-line processing at a speed that doesn’t limit their production yield.
The evolution of rugged edge nodes for the IIoT
NI recognises that the move toward the IIoT demands more rugged, high-end processing at the edge, as well as the increased use of vision. Therefore, NI’s latest addition to the NI Industrial Controller family offers the perfect combination of ruggedness and performance for edge processing. The IC-3173 is the most powerful Industrial Controller that NI has ever released. It includes a 2.20 GHz Intel Core i7 dual-core processor and Kintex-7 160T FPGA, which improves system performance by offering custom I/O timing, synchronisation, and control as well as image co-processing. Yet, the level of ruggedness is what makes this industrial controller unique. This controller builds on the ruggedness of the CompactRIO platform with an increased ingress protection (IP) rating of IP67, which ensures reliable operation in the presence of dust and water in accordance to IEC standard 60529. This makes this model ideal for spray-down and dirty environments such as manufacturing, test cells, or outdoor applications without the need for an additional enclosure.
With the addition of more and more subsystems - including complex vision systems - the need to converge these subsystems becomes more evident. Managing the integration of disparate subsystems (each with their own tools and programming environments) and inherent latency of industrial networks becomes challenging and costly as your systems become more complex. Because of its processing power and flexibility, the Industrial Controller enables more simplified measurement and control systems by allowing you to bring subsystems into one powerful, converged data acquisition and control platform. NI customers are already seeing the cost and efficiency benefits of bringing multiple subsystems into one platform.
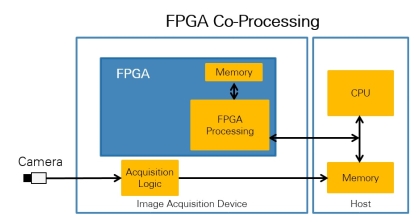
In FPGA co-processing, you acquire images using the CPU, and then send them to the FPGA via DMA so the FPGA can perform operations
“The NI Industrial Controller has a robust set of I/O resources that allows us to use one controller for every facet of our automation needs including vision, motion control, digital I/O, and testing,” said Jordan Larson, manufacturing engineer at Federal-Mogul Powertrain. “Furthermore, by utilising the built-in EtherCAT master for motion and conditioned I/O, we have greatly reduced the wiring and debugging time of the automation machines that we build. With the Industrial Controller family, we also have brought the cost per camera down tremendously compared to other cameras previously used for machine vision. Using NI’s Industrial Controllers we have reduced the number of components inside our machines and have all our control software on one platform, which was something we were unable to do previously.”
Optimising for machine vision
Although you can use NI Industrial Controllers in a wide variety of applications ranging from data acquisition to control, the connectivity options and the unique design make them especially useful in machine vision applications. These controllers support the GigE Vision and USB3 Vision standard with dedicated bandwidth, so you can select whichever camera meets your application needs without worrying about compatibility. In addition, the Industrial controllers feature a heterogenous architecture that combines a CPU and FPGA for advanced image processing. Using the FPGA as a coprocessor for machine vision applications can significantly decrease the processing time for a particular algorithm. Because FPGAs are massively parallel in nature, they can offer significant performance improvements, in some cases more than 10X, over CPUs for certain algorithms.
Easing distribution and synchronisation
One of the most complicated parts of commissioning a distributed data acquisition and control system is ensuring synchronised measurements and control over an entire system. To make this task easier, NI Industrial Controllers take advantage of the latest technology by incorporating Time Sensitive Networking (TSN) capabilities. TSN is an update to the Ethernet Standard that enables a shared notion of time across a distributed network over a single Ethernet cable, therefore minimising costly cabling and simplifying complex synchronisation architectures. This functionality is built into the programming API under the hood, so that you can get the functionality of TSN synchronisation with no extra work.
In addition to using TSN for controller-to-controller communication, you can also use this controller with the new TSN-enabled CompactDAQ chassis, released earlier this year, for distributed data acquisition.
The Industrial Controllers also have built-in support for hardware-timed IEEE 1588 Precision Time Protocol (PTP), which provides sub-microsecond synchronisation across many devices. Furthermore, because of the unique design, this same timebase can be shared with the user-programmable FPGA such that I/O and non-IEEE 1588 devices such as USB3 Vision cameras can be included in the network. Finally, the Industrial Controller supports IEEE 802.1AS and IEEE 1588, therefore it can act as a bridge between fully Time Sensitive Networks and more traditional IEEE 1588 networks. This ability to synchronise devices across multiple technologies provides maximum system flexibility.
The continued emergence of the IIoT requires powerful edge nodes for storing, processing, analysing, and acting on sensor data at the edge. NI’s Industrial Controllers meet industry needs for powerful, rugged edge nodes that are optimised for both distributed data acquisition and machine vision.
Contact Details and Archive...