Digital twin – it’s not just a buzzword
10 May 2018
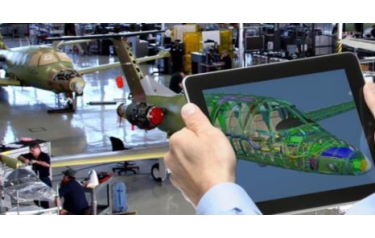
Digital twin (Credit: Siemens PLM)
Businesses are all facing the same issues - the need for innovation and the potential for market disruption. You have two choices when it comes to disruption; you’re either the one doing the disruption or you’re going to have to respond to a competitor disrupting your market. DPA & Connectivity Editor, Paige West, spoke to Tony Hemmelgarn, President and CEO of Siemens PLM Software, about how businesses can leverage the power of a digital twin to enable innovation and resolve disruption.
The digital twin isn’t a new concept, it’s essentially how you represent a physical product or a manufacturing process in a virtual way and the closer you get that representation to the original, the more value it provides. Siemens looks at all facets of this process, from ideation to realisation and utilisation. The ideation phase involves the upfront design of a product. At this stage you have to deal with all aspects of design from mechanical, electrical, fluids and software and think about how they all interact together. A digital twin has limited value if you can’t represent a product and production process holistically.
This is followed by the realisation phase which is where you bring the design to life - plan the factory, embed the robots etc. Once you’ve planned and built it you need to know how it’s working, so the utilisation phase looks at what’s happening with the product or manufacturing process. Through MindSphere, Siemens’ open IoT operating system, users can gather information on the automation equipment running on a factory floor and use that to effectively paint a picture. You’re taking data from the real world and feeding it into the digital twin.
Is the term ‘digital twin’ just a buzzword?
Customers are beginning to understand the importance of the digital twin because they’re being driven by the complexity and disruption they’re seeing. Complexity increases with every phase of the lifecycle, especially when you’re dealing with multiple products from various factories, suppliers, distributors, retailers etc. How do you gather all that data? How can you gain greater visibility into the supply chain and identify supplier quality issues?
Tony cites Dell as an example; Dell was looking to launch a new laptop but whilst it was in the prototyping phase, they discovered the LCD on the laptop was flickering. Instead of spending days, weeks or even months trying to isolate the problem, Dell implemented software from Siemens and within a matter of three hours they had access to billions of pieces of information and discovered a firmware issue.
The need to leverage data is growing rapidly but the idea of a feedback loop is still an early concept in people’s minds. That’s why data in a digital twin is so important; it won’t just tell you of any problems, it will show you why there’s a problem, and provide the capability to fix the problem. This really is the game changing value and will give you a deeper insight into your products and manufacturing processes.
Bridge the IT/OT gap
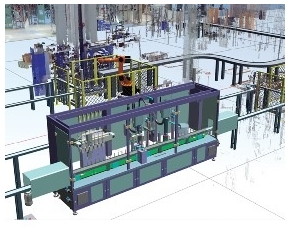
Digital twin (Credit: Siemens PLM)
The Information Technology (IT) and Operational Technology (OT) part of a company have long been separated - think of them as silos, with neither one knowing or understanding each other’s respective fields. In the process towards digital transformation, with the advent of physical machines and products becoming connected to the digital world, the IT and OT teams need to start working together. But how can you start to merge these two commonly disparate parts of a business?
The answer is simple – start weaving your digital thread and sew your silos together! Problems with a product no longer need to be thrown over to the manufacturing team; design engineers can make changes to their products and really begin to understand what impact that has on the plant floor. Most companies have a vision of where they want to be in this digital environment and a digital twin can help them get there.
It’s important to note this isn’t just about large aerospace, automotive or defence companies, but start-ups too. For example, Siemens has customers that are building drones to deliver medical supplies in Africa. For them, it’s about designing the drones using these simulation methods. How can I optimise it for battery life? How can I measure the payload and calculate the weight?
The future – for Siemens and its customers
In the last ten years, Siemens has invested over $10 billion into the software space - not just for use today but in preparation for the future and to keep pace with customer needs.
If companies don’t start embracing this digital transformation they are at risk of falling off the wagon, so to speak, in five to ten years’ time. Just think, if you can start to operate your manufacturing process faster than your competition, how long is it before they’re disrupted? If you start leveraging the power of the digital twin into your whole design process, how can your competitors compete? This innovative area of digital transformation really is the place to be at the moment.
Contact Details and Archive...