Oil and gas industry goes digital
05 July 2018
Robotic Drilling Systems AS (RDS) develops fully automated operating robots for use in onshore and offshore oil and gas drilling. The aim is to replace cost-intensive manual labour by robots, which will drive down operating costs and eliminate the need for dangerous tasks to be performed by humans in the future. In terms of its drive and control technology, RDS works in close cooperation with Siemens. The company also uses components from the Siemens automation portfolio in its robots.
The integrated solution used enables the entire drilling process to be automated, marking a major step towards digitalisation in the oil and gas industry.
The environmental, health and safety regulations applicable to personnel and operating equipment used in the production of oil and gas are understandably extensive. In addition, high operating costs are placing platform operators under considerable economic pressure. The company RDS, founded in 2005, has found a way to ease these pressures with the development of a new solution for the oil and gas industry. The system basically consists of drill floor robots, robotic roughnecks, multi-size elevators and robotic pipe handlers. This allows potentially risky manual tasks performed on the drilling platforms to be executed by machines, boosting efficiency and improving both process quality and repeatability. Siemens technology is used for the drive systems, process visualisation and smart communication between the control room and the robots, and also between the robots themselves.
Distributed control and visualised processes
Every robot has its own digital control system. In addition, in the control cabinet, Simatic industry PCs use Simatic Step 7 software to read sensor signals, translate process commands into motion control sequences and coordinate cooperation between the robots. On the machine level, the drives comprise Sinamics S120 converters, Simatic S7-300 controllers and the Simatic ET 200 distributed I/O. This distributed machine control system is used to visualise all mechanical processes taking place in the drilling platform both digitally and on Simatic HMI (Human Machine Interface) panels in the control room by means of WinCC Advanced. This enables the drilling technicians to control and monitor running operation without the need for manual intervention. Communication between the control room and the robots is secured by components from the Scalance S and Scalance X family, which are robust and so ideally suited for use in inhospitable environments. The Scalance X switches are also in compliance with a whole range of different standards which are a critical requirement to their use in the oil and gas industry.
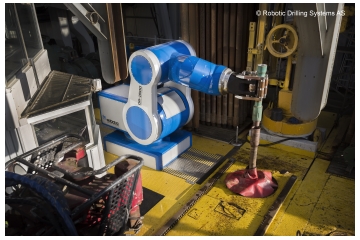
Operating robots boost efficiency and minimise risk
Reliable, secure communication enabling trouble-free data transfer along the entire oil and gas production value chain is vital to permit its digitalisation. The robot solution developed by RDS also replaces labour-intensive, costly manual processes by the use of operating robots which interact seamlessly together. This means that platform operators benefit not only from lower costs, but also minimised risk for personnel as well as greater availability and improved drilling rig reliability. All these factors support greater efficiency in the field of oil and gas production.
Contact Details and Archive...