Get smart – the pumping operations enjoying a digital makeover
11 September 2019
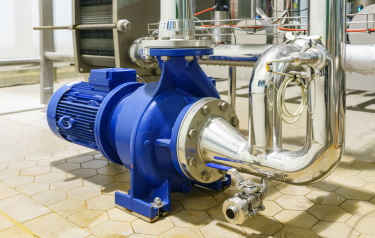
Shutterstock image
Lesley Eaton, Marketing Executive for SEEPEX, outlines some of the forthcoming developments to improve progressive cavity pump performance and maintenance, as well as process performance. Find out how you can climb the digital hierarchy…
The 4th Industrial Revolution is changing manufacturing in the UK. Whatever latest buzzword is being used to describe it – connectivity, digital transformation, Industry 4.0, 4IR – there are very few companies who aren’t aware of its existence.
In fact, across the UK in general, the digital revolution is moving forwards at an impressive rate. Latest figures from EEF, the manufacturers’ organisation, show that many firms are now moving on from simply understanding the concept of 4IR and are actively investing in it to improve their processes and increase their productivity. Just 27% of manufacturing firms surveyed are still at the ‘conception’ phase, while 39% have now reached the ‘evolution’ stage and are optimising their current business practice with smart technology.
With this in mind, Lesley Eaton, Marketing Executive for progressive cavity (PC) pump specialist SEEPEX, outlines some of the forthcoming developments to improve progressive cavity pump performance and maintenance, as well as process performance. Find out how you can climb the digital hierarchy…
Pump and process control
Pumps are becoming ‘smarter’ with increased integral sensors and connectivity, enabling local control and/or integration into higher control systems. Equipment manufacturers can contribute to the system engineering and commissioning requirements by supplying a solution, not just a pump. For example, smart dosing pumps comprise a progressive cavity pump with drive and control software, as well as flow rate sensors and optional safety functions. The control system is integrated into the pump, providing both modular automation and enabling vertical integration. The constant real-time feedback compares the data from sensors with parameters determined for the process, and automatically adjusts the pump speed as process conditions change. This self-regulating pump reduces maintenance requirements and ensures cost efficient system operation.
Condition and process monitoring
The aim of plant operators is to optimise process control and reduce costs. Knowledge of the pump’s operating status is essential in order to increase the efficiency of pump control and to plan maintenance intervals more effectively. Specialised devices are available which turn pumps into intelligent field devices that continuously monitor themselves and the process in which they operate. Pump monitoring systems are designed to observe operational information such as flow rate, temperature, pressure etc in real time, thus recording the operating conditions and efficiency of the pump. Systems of this type can provide users with history and trends for performance analysis and for process optimisation. Deviations from set values trigger alarms, notified by SMS or email push notifications to mobile devices, reducing standard inspection tours and providing greater safeguards for critical production processes. The analysis of data in this way also enables pump maintenance demands to be predicted and service intervals scheduled accordingly.
Connected services
By connecting pump monitors and automation equipment, data can be transferred to cloud-based online services. This connectivity is the basis for Industry 4.0 and provides the information needed to improve equipment and process performance. Companies with connected services can benefit, for example, from remote monitoring and data analytics of all equipment. The suppliers’ cloud services can collect data from the field and make it available everywhere – retrievable by the user at any time and from any location. SEEPEX connected services, for example, compare the data received from their pump monitors with the previously defined operational specifications to determine deviations from the optimum performance. This deviation is communicated to the user to enable corrections to the process to be made.
The use of API (application programming interface) software can also interlink equipment from different suppliers to produce a general process overview and enable whole process optimisation.
Predictive maintenance and service digitalisation
Data collected by pump monitors using Bluetooth, Wi-Fi or SCADA systems can be analysed against historical pump trends and specifications to identify when maintenance is needed – predictive rather than scheduled. Connected services can link this data collected via the cloud to the manufacturer to identify which parts are needed. The ERP (enterprise resource planning) system then ensures the correct parts are available, even arranging shipment to site, providing a fully automated diagnostics and spare parts ordering system for customers. In this way, equipment and spare parts are not replaced unnecessarily, saving on both material and labour costs.
On-site technicians can use service apps to provide virtual reality instructions for pump maintenance via smartphones or mobile devices, which can be invaluable to service engineers on site. Similarly, access to service and instruction manuals, spare parts lists, chat service lines and ordering systems can all deliver maintenance efficiency. For example, SEEPEX pumps have QR codes which, when scanned with a smart phone camera, uniquely identify the pump and generate a spare parts list and O&M manual if needed. Using the app, spare parts quotations can also be requested. Apps of this kind offer on-site digital solutions to provide instant operational information and simplify the supply chain.
Contact Details and Archive...