Network tests pave way for smart factories
08 June 2021
5G has everything future smart factories need for wireless connectivity, but network tests are essential.
3GPP Release 15 standardised 5G technology and is the basis for current 5G networks. Significant improvements in latency, network synchronisation and industrial Ethernet network integration are expected from Release 16, which the 5G Automotive Association (5GAA) and the 5G Alliance for Connected Industries and Automation (5G-ACIA) have played a strong role in shaping. The release helps 5G evolve into a technology suitable to meet smart factory requirements (Industry 4.0). These requirements are characterised by data driven real-time control of all processes and the quick and flexible reconfiguration of production lines. Full connectivity of machines, people, plants, logistics and products is only feasible with wireless technology. Fast wireless 5G based links will be the nervous system coordinating the complex factory structure. Even a brief data flow interruption can have serious consequences and high costs, meaning the wireless network must be designed, set up and monitored with great care. The process requires several phases (including testing), as described below.
Vital KPIs for mobile networks in wireless connected factories
A smart factory is a critical environment that must fulfil strict requirements for machine connectivity and reliability as well as data security and human safety, especially if connectivity is provided by wireless technologies.
Redundancy is a proven way to increase reliability. Every location in a smart factory must be served by at least four wireless access points. On-site tests are the only way to verify this access, not only upon installation but after every machinery reconfiguration or change to the building layout, since structural changes can impact the propagation conditions of radio waves.
Reliable ubiquitous wireless accessibility is necessary but not sufficient for trouble-free operation. Another requirement is the proper performance measured not only in achievable data throughput but also – and often more importantly – latency or the time needed for a signal to pass through the system. The latencies of previous mobile communications technologies, up to and including 4G, were not short enough to meet real-time control requirements. This is no longer true for 5G, which has latencies of a few milliseconds.
Latency comes in two forms: round-trip and one-way (Fig. 1). Augmented or virtual reality use cases need short round-trip latency for very quick image content updates when people wearing AR/VR glasses move their head, to keep the merged data consistent with the live image. By contrast, real-time control of a connected machine requires low one-way latency. Control commands, for example a stop command for a robot, must lead to immediate action.
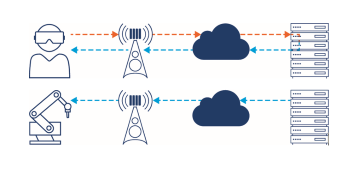
Figure 1
The five phases of network testing
When planning a factory as a whole, wireless networks are implemented in phases based on a five-phase test plan. Fig. 2 shows the first four phases for verifying that the network fulfils strict reliability and performance requirements.
Phase 1: Rollout preparation
In Germany and some other countries, 5G frequencies are reserved for campus networks or private networks and factory operators can apply to use these frequencies. Setup and operation of the network can be organized inhouse, but is usually done by service providers. In countries without dedicated campus frequencies, factory connectivity involves booking resources from a major network operator, who in turn consolidates their network around the factory or installs additional base stations in the factory to meet requirements.
If the network uses campus frequency bands, the spectrum needs an initial check for interference. Experience shows that this cannot be taken for granted with a newly assigned and previously unused spectrum. R&STSMx6 network scanners, R&SFPH/R&SFSH handheld spectrum analysers and R&SMNT100/R&SPR200 portable test receivers perform the necessary measurements.
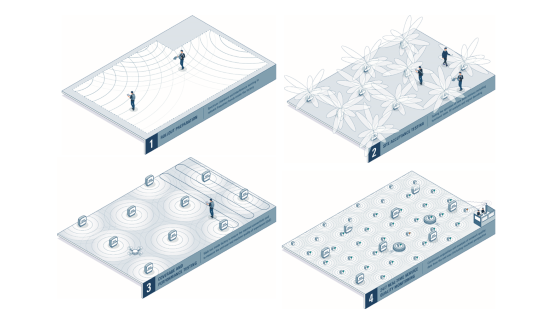
Figure 2
Phase 2: Site acceptance testing
The second phase involves testing and validating newly deployed base stations. This includes simple functional tests such as download/upload tests, round-trip latency measurements, over-the-air (OTA) RF spectrum analyses and signal decoding to verify PCI, SSB and SIB data for 5G and LTE anchor signals.
Signal decoding also helps troubleshooting specific parameters in case of problems or unexpected results.
The Rohde & Schwarz product portfolio has the right instruments for these tasks. QualiPoc Android, a smartphone-based measurement software, evaluates the mobile network service from the user perspective with functional tests (DL, UL, ping/TWAMP). The R&SSpectrum Rider FPH handheld spectrum analyser is ideal for OTA spectrum measurements, while the R&S5G site testing solution provides a comprehensive mobile network situational overview that allows quick identification of any weaknesses or problem areas.
Phase 3: Coverage and performance testing
Now comes the real test. The aim is to make sure the network delivers the required performance throughout the entire factory.
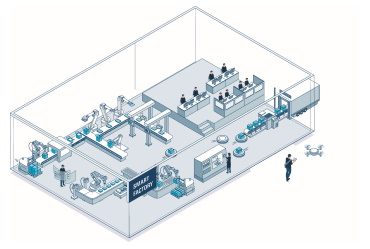
Figure 3
R&STSMx6 network scanners measure over the entire factory site to see how many different network access points have good reference signal received power (RSRP) and good quality as signal to interference plus noise ratio (SINR) at every location. As previously mentioned, at least fourfold redundancy is desirable.
QualiPoc Android can test the real-time capability of the connection by combining the emulated traffic profile, latency measurement and transmission quality in a single interactivity test (see box out).
The R&SSmartONE real-time optimisation software enables immediate visualisation of measurement results and targeted improvement of problem areas.
Phase 4: Service quality monitoring
Phase 4 measurements are necessary in factories where the wireless network is critical infrastructure where malfunction would result in large profitability and productivity losses. This means the factory owner needs a clearly defined service level agreement (SLA) with their network operator and the ability to continuously check compliance with the SLA. Custom RF sensors are distributed throughout the factory and in automated guided vehicles (AGV) and autonomous mobile robots (AMR). They periodically measure connection quality – including latency – at every location and report the results to the monitoring centre (SmartMonitor), where they are visualised on a real-time dashboard. Tools like SmartAnalytics offer more detailed offline data analysis. The software uses machine learning to identify trends and anomalies and promptly indicates aberrations so that preventive measures can be taken before the fault case actually occurs.
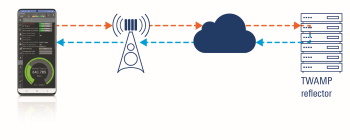
Figure 4
Phase 5: Verifying prescribed compatibility with the outside world
Completion of phase 4 marks the end of the setup process and the network is operational. The final task is to ensure compliance with the license conditions for private networks that specify leakage signals outside the intended coverage area must remain below defined limits. This helps prevent interference with any neighbours using the same frequency band or an adjacent frequency band. Factory owners are recommended to check compliance and can do this with a walk test solution such as the R&SFreerider 4 or a network scanner mounted on a drone (Fig. 3).
Summary
Several industries will need to convert their current factories into smart factories. Conventionally organised operations will have difficulty competing with the flexibility and cost advantages of the new generation of factories. One feature is complete connectivity of equipment with low latency (5G) wireless communications. The right T&M support makes setting up and operating these networks easy. The Rohde & Schwarz product portfolio offers network operators and factory owners everything they need.
Tutorial videos and more information are available on a dedicated smart factory webpage: www.rohde-schwarz.com/mnt/smart-factory
Digression: A new method for measuring network performance
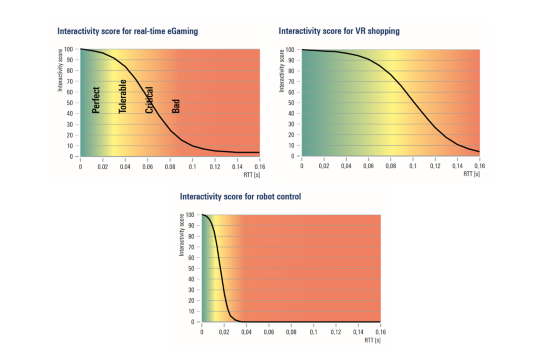
Figure 5
Ensuring superior network performance with full coverage is essential in factories. The latency and data throughput must meet the minimum requirements everywhere in the coverage area. A new method implemented in the smartphone based QualiPoc Android software solution makes such measurements easy and reliable.
Latencies are conventionally measured with ping echoes. Ping is part of the internet control message protocol (ICMP) used to exchange diagnostic and error messages in computer networks. However, the ping method has inherent accuracy shortcomings, which impact low latencies such as those needed in 5G factory networks. It is not suited for precise measurements of very low latencies and cannot emulate traffic patterns. A better method is based on the two way active measurement protocol (TWAMP), which the Internet Engineering Task Force has specified for measuring end-to-end performance between two nodes of an IP network. What TWAMP can do in a measurement application strongly depends on its implementation. The Rohde & Schwarz solution is part of the QualiPoc Android measurement software and computes a meaningful overall score from several metrics. This innovative method has been proposed for standardisation.
The QualiPoc smartphone sends a stream of application-specific data packets via the UDP transport protocol emulating a realistic traffic profile of a specific use case class to a TWAMP capable server (TWAMP reflector), which immediately sends them back (Fig. 4).
The QualiPoc software determines the round-trip latency from reflected data, its range of variation (minimum and maximum measured values) and the packet error rate, and combines these three KPIs to form an interactivity score for this specific use case class. This is a scalable QoE model that can be tailored to different application classes. Fig. 5 shows example score curves for example use cases.
The software is attractive not only for service measurements, but also for every real-time wireless application. Suitable profiles are being developed in cooperation with the respective industries.
Contact Details and Archive...