Sponsored Article
Why tailored, sustainable, and connected conveying equipment is a logistics industry differentiator
Author : Mark Yeeles, Vice President of Industrial Automation at Schneider Electric
13 October 2021
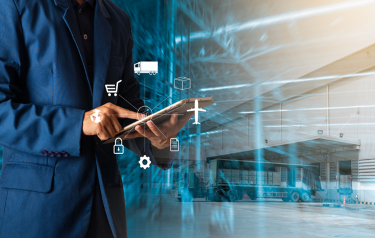
(Shutterstock image)
The World Economic Forum expects that a more sustainable, circular economy could be worth $1 trillion worldwide by 2025. As green products continue to gain steam, conveying equipment and logistics industries need to embrace new approaches such as "embedded sustainability" – incorporating environmental, health, and social value into core business activities without a trade-off in price or quality.
Achieving this goal requires a proactive mindset to determine the right actions to take to improve the operation’s sustainability concerning all emission scopes. Scope 1 (direct emissions from sources an organisation owns or has control over), Scope 2 (indirect emissions associated with the production of electricity), and Scope 3 (emissions related to supply chains).
Beyond the sustainability challenge will also be the transition from traditional siloed supply chain approaches to a focus on real-time, end-to-end supply chain visibility. Technology investment decisions that involve the digitisation of operations, material handling firms must also consider both the origins of the products that come into their distribution centres and the logistics that determine the sustainable delivery of those products to the end consumer. The ability to link consumer data back to the supplier of suppliers requires both centralised control and end-to-end planning tools.
Technologies such as supply chain control towers, which currently serve the role of providing connected, personalised dashboards of data and the tracking of key business metrics and supply chain events, will continue to evolve. They will begin to address either the mitigation or the management of events happening upstream (e.g., supply shortages) and help better manage the reaction to and reception of end products downstream (e.g., consumer buying habits).
Supply chain digitisation and customisation creates new OEM opportunities
For the OEMs who support the logistics and conveying equipment industries, success or failure hinges on innovation, reduced machine design time, energy-efficient machines, and lowered manufacturing costs. These business goals are achieved through the acquisition, design, and assembly of optimised and flexible solutions. Today, a key-differentiating factor is a machine system’s ability to continuously adapt to changes required by the end users.
Fluctuations in demand, different user preferences, and mass-customisation of packaged goods are a few drivers of this change. Embedding this adaptability is difficult because machine system designs must also accommodate rapid production speed, high-quality output, and be flexible enough to manage varying specifications, all without compromising the machine operator’s safety.
Thanks to these challenges, the rising digitisation of supply chain processes and the increasing level of order customisation and personalisation can generate more business opportunities for OEMs. If a machine can generate a product based on a single request and is capable of adapting to that request, then that machine owner possesses a clear marketplace advantage. Digitisation is the catalyst to overcome the perceived complexity of being able to deliver mass order customisation.
Partnerships and more open technology linkages act as modernisation catalysts
As the industry evolves, no one organisation can manage and integrate this new wave of digitisation on its own. For a sustainable future, advanced automation and digitised conveying equipment systems are no longer an option. They are a prerequisite for remaining competitive.
As the tactical challenges of increasing labour costs, rising eCommerce-driven fast delivery expectations, safety concerns, and an increasing need for robots in warehousing and distribution centre facilities present themselves, strong partnerships will be critical to achieving marketplace success.
Organisations such as Schneider Electric offer the logistics and material handling industries, and the OEMs who support them, the solutions and expertise needed to take on these tactical and strategic challenges. Gartner recently ranked Schneider Electric #4 on its annual Supply Chain List of the Top 25 global supply chain leaders.
Schneider Electric experts work with supply chain partners to extract energy savings and sustainability benefits throughout the entire product creation, delivery, and support lifecycle. 73% of Schneider Electric’s investments are directed towards developing newer and even more sustainable solutions.
This kind of commitment helps logistics and material handling firms to seamlessly integrate OT automation solutions with IT to extend the power of data analytics. The improved linkage between the digital order entry, warehouse and distribution facility inbound and outbound traffic management, robotics deployment, and shipment tracking results in several business advantages for end users.
Contact Details and Archive...