Comprehensive digital twin turns complexity into a competitive advantage
01 December 2021
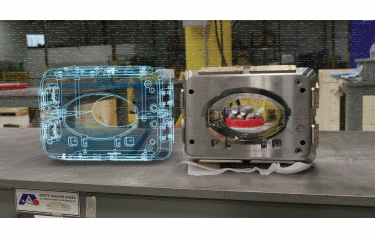
Figure 1: Digital twin example
Complexity is disrupting practically every organisation and industry: complexity of product development, manufacturing processes and product utilisation data. Although this can be overwhelming, those organisations that embrace this complexity can use it as a competitive advantage to outperform their competitors. The key is digital transformation.
Digital transformation enables companies to manage complexity, integrating all parts of the business, to turn data into value at all stages of the product and production lifecycles: design, realise and optimise. And the comprehensive digital twin is the crucial, foundational capability to speeding this digital transformation, acting as a catalyst to a fully digital enterprise.
The term ‘digital twin’ seems to be everywhere these days but with slightly different meanings. Yet, these various digital twins tend to share a common characteristic: the digital twin as a connected 3D design or simulation model of the product (Figure 1). This is because, at its heart, the digital twin is a virtual representation of a physical object that evolves and changes over time along with the product it represents. As such, the digital twin merges the virtual and real world, blurring the boundaries between engineering and process domains.
At Siemens, our definition and understanding of the ‘digital twin’ is both broader and more precise. Some believe that a product can have multiple digital twins throughout its lifecycle. Our perspective is that there is only one digital twin of a product that includes and supports the numerous lifecycle phases and respective models of actual product behaviour. This comprehensive digital twin has the following characteristics (Figure 2):
• Offers a precise virtual representation of the product or process flow that matches the exact physical form, functions and behaviour of the product and its configurations.
• Participates across the product and process lifecycle to simulate, predict and optimise the product and production system used to create the product.
• Connects real-world operational data back into product design and production over the lifetime of the product to continuously improve quality, efficiency, and quickly respond to customer demands or market conditions.
The comprehensive digital twin of today’s complex, increasingly ‘smart’ products include all cross-domain models, such as CAD or CAE, software code, chip designs, wire harness models, bills of process and materials, and more. This digital twin of the product evolves and is enriched over time as configurations are refined, interrelationships specified, test results are gathered and engineering changes are enacted. Furthermore, IoT capabilities and data analytics create a closed-loop with the production system and the product in the field, providing an integrated feedback system to validate, compare, optimise, and even control behaviour, bi-directionally, between the physical product and its digital twin.
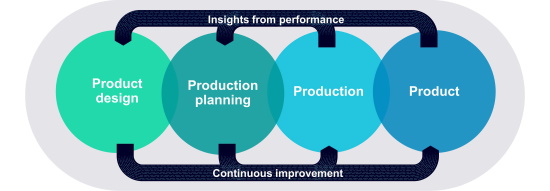
Figure 2
Why is this important? Nearly every product and process is becoming more sophisticated and more complex as customer demands for greater performance, new features, higher quality and personalised experiences grow. Companies must shorten overall design and manufacturing lifecycles, while managing increasing product complexity and remaining adaptive to market conditions. The comprehensive digital twin can empower companies as they pursue these goals by extracting value from the terabytes of data generated from connected product and process lifecycles. As a result, it can help companies break down the silos that isolate information, processes and people across the enterprise.
Moreover, the comprehensive digital twin enables your company to design, build and optimise next-generation products faster and cheaper than ever, with fewer prototypes, fewer tests and less waste during production. But, it’s about more than just product innovation. The comprehensive digital twin also unlocks a new level of process innovation, allowing companies to take new approaches to their core business models and processes – turning the companies of today into the digital enterprises of tomorrow. And our customers are already taking steps in this direction.
New business models for the industries of tomorrow
Tomorrow, companies will need to evolve their core business processes across the design – realise – optimise flow. Among our customers, we have already observed several examples of companies taking leadership in the transformation towards digital enterprises, relying on the digital twin to establish new, more effective business approaches and models.
Design
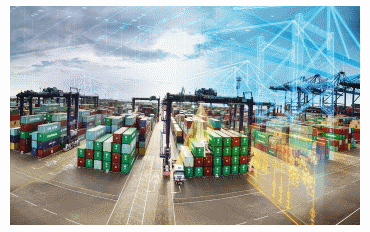
Figure 3
Konecranes, a Finnish company that manufactures some of the world’s largest cranes, leveraged digitalization to accelerate their design cycles. Previously, Konecranes’ design, simulation and prototype testing groups all operated in silos. These silos created problems during the synchronisation of engineering data and versions, leading to inefficiencies in the turnaround of product designs. To resolve these issues and eliminate barriers between engineering departments, a role-based digital twin application was developed to aggregate data from each department (Figure 3).
Konecranes’ digital twin provides a synchronised and holistic view of the overall product design lifecycle, including simulation and prototype testing results. This robust digital twin includes design requirements, engineering data and various simulation models and their relationships among engineering domains. Meanwhile, connected prototypes feed sensor information back into the design and simulation teams to continuously improve product models and their reflection of real-world behaviour. With this comprehensive digital twin backbone, Konecranes has accelerated its product design and development process by reducing prototypes and increasing traceability, while simultaneously improving product quality and lowering the cost of development.
Realise
Next, Vinfast, Vietnam’s first volume automotive manufacturer, is taking advantage of a connected digital twin across both design and manufacturing, giving them an immediate competitive advantage in the global automotive market. This digital twin includes lifecycle management solutions to support cost and value engineering, industry-leading digital manufacturing software and a manufacturing execution system layer. Lifecycle management software connects the comprehensive digital twin to a consistent digital thread to help the company increase the speed and flexibility of product development, optimise manufacturing processes and use the insights gained from product and plant operations to improve future performance for both design and manufacturing.
In particular, Vinfast leveraged the digital twin during the plant design and commissioning phase to design, commission and build a state-of-the-art manufacturing facility (Figure 4). The comprehensive digital twin enabled Vinfast to complete designs across multiple domains - including mechanical, electrical, software, production and planning – and virtually commission both the plant and the production lines within the factory – reviewing and optimising manufacturing operations in the virtual world before putting an actual machine on the factory floor. This digital manufacturing design and commissioning flow enabled the automaker to create their new facility in just 21 months, instead of to the usual five years.
Optimise
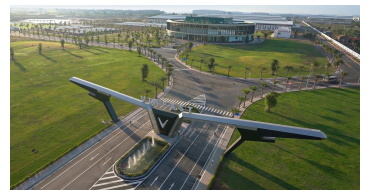
Figure 4
Finally, Renom, a leader in providing services for the renewable energy market, uses the comprehensive digital twin to optimise infield wind turbine performance and energy yield. Maintaining and optimising remote wind farms is often challenging, complex and costly. One critical challenge is predicting the remaining useful life of major components, like the gearbox. The typical gearbox in a wind turbine has a lifespan of three to five years and will need to be repaired or replaced several times over the service life of a wind turbine. By predicting the remaining useful life, Renom can optimise maintenance and extend the life of turbine gearboxes and other critical components, reducing costs and preventing unplanned failure in the field.
Renom achieves these outcomes through a single user experience that allows operators access to real-time performance data from individual turbines or the entire wind farm. This interface is powered by a comprehensive digital twin that is comprised of several models such as the precise 3D definition and build materials of the turbine and its components; simulation models of key subsystems and components; and specific service requirements, schedules and even the availability and cost of spare parts. The solution also accumulates industrial IoT data and load factors to enable the tracking and monitoring of the remaining useful life of components at various levels, enabling Renom to proactively perform services and maximise energy yield.
Reaching the digital industrial future
Companies of all sizes and in all industries are grappling with increasing product and process complexity and customer demands for quality, capability and customisability. In the face of new and mounting pressures, companies are searching for ways to transform their core processes to deliver advanced, personalised products to their customers at accelerated speed.
The comprehensive digital twin offers the straightest path to achieving these goals. The comprehensive digital twin encompasses the complete lifecycle of the product and the plant, enabling companies to reconcile efforts across multiple engineering disciplines, manufacturing and over the lifecycle of the product, creating a continuous closed-loop between the real and digital worlds. Such a connected, digital flow will prove crucial to maintaining a competitive edge and ensuring success in the industries of tomorrow.
Contact Details and Archive...