Sponsored Article
OEMs' critical role in creating more agile conveying equipment and sortation solutions
Author : Mark Yeeles, Vice President of Industrial Automation at Schneider Electric
03 December 2021
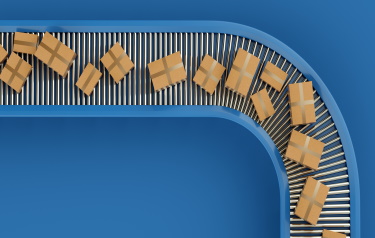
(Shutterstock image)
The global conveying systems market is expected to expand from $5.2 billion in 2019 to $7.4 billion by 2027. Over the projection period, this represents a 4.5 percent CAGR. OEMs that successfully design and develop the machinery that will power this expansion will need a better grasp of how trends like digitisation and the global pandemic affect the logistics industry and conveying equipment systems.
The pandemic has disrupted "business as usual" for thousands of logistics companies around the world. As distribution centres scurry to increase agility and resilience while navigating unconventional working conditions and unpredictable supply chains, a new mindset for survival has emerged: accelerate the push toward digitisation.
Indeed, according to a recent McKinsey Global Survey of executives, their companies have "advanced the digitisation of their customer and supply-chain contacts, as well as their internal operations by three to four years."
Why? The capacity to automate selecting, sorting, and conveying activities to better satisfy rapid demand has proven to be a lifesaver for businesses caught in the midst of pandemic-driven market shifts. However, COVID-19 will not be the last problem industries will face. Moving forward, supply chains that are nimble enough to weather both unanticipated crises and rapidly changing market conditions will be a key competitive difference.
Save labour costs and reduce lead-time with modern conveying equipment
For many logistics organisations, a key goal is full material handling automation and product movement. Process automation of order entry, warehouse and distribution facility inbound and outbound traffic of goods, robotics deployment, and shipment tracking are all considered key stepping stones towards digitisation of these businesses. To accomplish these transformations, logistics organisations are counting on their OEMs to develop automation solutions that result in substantial process efficiency improvements.
This new world of logistics, robotic solutions, and more open automation systems will create additional opportunities for high-value engineering. Until now, traditional conveying equipment systems required a series of high volume, repetitive, manual programming tasks, in order to enable interoperability between heterogeneous subsystems. Under these circumstances, logistics firms were hesitant to pay high rates for work that failed to add any real value. End users are also more likely to avoid upgrading their systems because of concerns over high cost, time, and risk.
New software-driven automation engineering, however, adds value to the integration process by drastically minimising manual, low-value engineering steps. Traditional barriers can be overcome by promoting software-centric and asset-centric automation, by active wrap and reuse of existing systems, and by introducing a new generation of “plug and produce” portable and interoperable solutions that are far less costly to implement. These solutions optimise IT/OT convergence and set the stage for self-configuring, self-healing and faster retooling systems that drive speed and agility.
Evidence of early successes can be found in vast warehouses near major towns, manned by expansive networks of conveyors, or armies of robots that pick products from thousands of bins and assemble those products into a secure, ready-for-delivery package. Such warehouses are justified and cost-effective because the need for manual labour has been significantly curtailed, while the distance between consumers and their products has been shortened.
Automation: Saving time and money
The fully articulated legacy robots that logistics companies have in place are imposing work cycle speed constraints as they try to speed up their operations by deploying digital conveying equipment systems.
As a result, makers of conveying equipment systems are now focusing more on delivering the components needed to deploy contemporary pick-and-place solutions. Delta robots (parallel robots with three arms connected to universal joints at the base), cartesian robots (an industrial robot with three principal axes of control that are linear and at right angles to each other), and SCARA robots (for pick-and-place or assembly operations requiring high speed and accuracy) are examples of technologies that address these current needs for faster speed and higher accuracy. Schneider Electric's expertise help OEMs minimise time-to-market by integrating the drive, controller, mechanical, and motor sections of these robots into bigger conveyance machines. As a result, end users benefit from more agile, adaptable solutions.
Contact Details and Archive...