Exploring the open future of distributed control
Author : Luis Duran, ABB
02 November 2023
Luis Duran, Global Initiatives and Strategy Manager, Distributed Control Systems for ABB, envisions a future process control architecture that will help unlock the full potential of plant data and the industrial Internet of Things.
The industrial Internet of Things (IoT) is already starting to deliver real benefits for manufacturers, thanks in no small part to the increased computational power that companies can tap into via cloud and edge computing.
Other technologies are also playing an important role in this transformation. Businesses can gather huge volumes of data with an unprecedented degree of granularity. And, thanks to the power of AI and machine learning, they can analyse that data in near real time and so unlock a wide array of benefits across almost every area of the business. Rewards range from the ability to implement predictive maintenance to a hugely accelerated response to changing demands.
The processing power needed to deliver these new, data-based applications may be cloud-based in central server farms or distributed in edge computing devices, perhaps on-premise. However, at the heart of the data flowing into, out of and around, a manufacturing plant sits the distributed control system (DCS).
Traditional DCS technologies can make it difficult for production lines and processes to engage fully with data flows across the wider IoT, especially since external applications must rely on protocols and interfaces that are not typically available on existing systems. This may be because these systems are proprietary, for example, or for security reasons. Whatever the case, the resulting data silos can leave users struggling to reap the rewards of emerging, data-based solutions.
Opening up
Happily, ABB believes there is an approach to future control systems that can effectively bridge this gap between the DCS and the wider IoT.
One of the most powerful initiatives spearheading this new process control architecture is the Open Process Automation Forum (a.k.a. OPAF) hosted by The Open Group. OPAF is a global consortium of more than 900 organisations, including end users, product and solution providers, integrators and academics. Together, they are working to define a set of standards to enable the development of open, secure, and interoperable process control architecture.
Meanwhile NAMUR – a global consortium of process industry end-user organisations with roots in Germany’s chemical industry – has also defined a new open architecture model (NAMUR Open Architecture, or NOA), defining an open and secure application layer with access to relevant information, while preserving the integrity of the core process control in the form of a DCS.
Both bodies advocate an approach that effectively segregates core control and automation functionality from a broader digital environment, where non-time-critical monitoring and optimisation functions can take place.
Dual domains
At the heart of the new architecture sits the robust, evergreen core. This will be designed to allow DCS systems to evolve continuously by making a continuous series of incremental changes to meet changing needs, rather than deploying new infrastructure every few years. In other words, investments will be protected, because companies should not need to retire their existing DCS installed base and start again from scratch whenever new IoT technologies arrive.
Meanwhile, the extended, digitally-enabled environment facilitates faster innovation and continuous performance improvements. This is where the next generation of applications based on AI and data analytics will reside. The aim is to grant them secure access to a constant stream of high-quality data from the core and elsewhere. Digital solutions can then transform that data into meaningful insights that enable better business decisions.
Modular automation
The concept of modular automation applies across both domains.
In the core, there have been industry-wide efforts to shift away from the conventional DCS model of monolithic, strongly intertwined automation systems that are designed to control an entire production site. Instead, the new, open standards favour the use of flexible, service-oriented modules that are each designed to carry out a relatively narrow set of functions. These ‘plug and produce’ modules fit together via standardised, secure communication interfaces to produce complex site-wide control schemes.
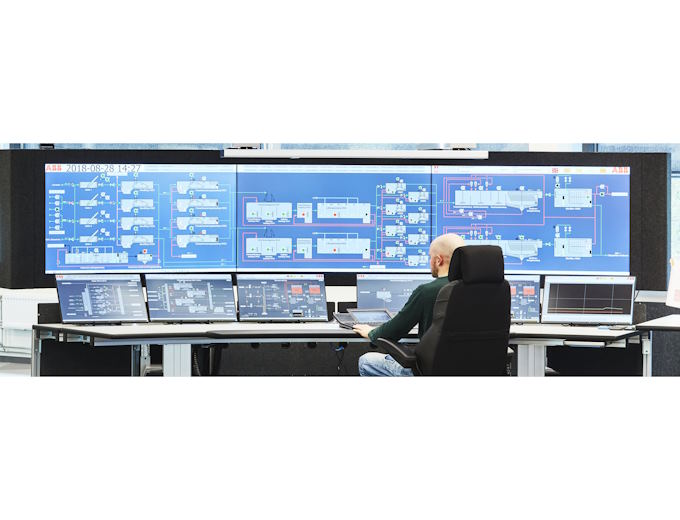
ABB Ability System 800xA
This modular concept aims to deliver faster process implementations, unlimited capacity scaling and speedier process adaptations.
Similarly, the extended digital environment is made up of virtual, modular functional units bounded by cybersecure interfaces based on OPC UA (Open Platform Communications Unified Architecture) standards. These modules are automatically orchestrated to meet a range of performance and security expectations according to their function.
Decoupling HW and SW
The modular approach effectively decouples DCS hardware and software, since process controller and application software exist as functional modules, rather than being programmed to work with a specific piece of hardware. These modules can be deployed flexibly wherever they are needed, whether that is across purpose-built and industrial PC controllers, edge devices, on-premises servers, or cloud platforms.
Automated systems will be necessary to orchestrate all these modules and balance the load across different hardware resources. Without this additional layer of automation, the need for system orchestration could represent a big change in the way that users of future process automation systems would need to work. Unlike IT departments, operations engineers are typically focused on running their processes, not managing the systems that control them. Automated orchestration solutions can carry out these system management tasks largely out of sight while ensuring that operators retain full control over processes.
Each module can be easily modified without impacting on overall operations. This means that control system users should be able to take advantage of future technologies and solutions, with minimal disruption to their existing systems. It also means that each organisation can retain their overall infrastructure while adopting new technology at their own pace as needs dictate.
Security matters
Crucially, while it offers users the flexibility and freedom needed to unlock the full power of plant data, this modular, dual-domain approach is also very secure. It effectively shifts the job of enforcing authentication and authorisation away from the network perimeter. Instead, a zero-trust approach must be adopted at the core. Components will be required to prove their identity and originality digitally, as well as their authorisation for specific tasks.
Design first, deploy later
As well as improving day-to-day operations, decoupling automation hardware and software can also make life easier at the design and engineering stage of projects. Thanks to a combination of virtualisation, emulation and simulation technologies – all implemented in the cloud as a digital twin – engineers can perform virtual application testing and commissioning before doing anything that could interrupt production on the physical factory floor. This virtual commissioning can identify potential issues and deliver a smoother, faster start-up.
Innovate to accumulate
Today's DCSs already enable many low-level industrial processes to run without human intervention under normal conditions. Human decisions are often needed only to deal with unusual situations and the complex tasks associated with them. In future, more autonomous automation means progressively handing over more and more of these complex tasks to the DCS. That will only be possible if users are able to take full advantage of emerging AI and machine learning capabilities beyond the core control system.
Evolving control technologies to integrate more easily with applications in the cloud or on edge devices will therefore play a key role in realising this IoT-based vision of smarter and more productive industrial facilities.
Contact Details and Archive...