In the zone: Why Zone 2 needn’t be “scary” or “painful”
Author : Tony Coghlan, Turck Banner
08 May 2025
What is Zone 2, why is it perceived as “painful”, and what solutions are available for making your ATEX Zone 2 less painful?
IP67 remote I/O
With IP67 compliance in mind, where a device or product is dust-tight and protected against temporary immersion in water, a remote I/O approach can bring several benefits to operations, including in Zone 2 settings. For one, IP67 remote I/O systems with through-bussing enable the connection of I/O modules in harsh environments.
Using a bus structure allows for multiple I/O modules to be connected along a cable, extending the reach of the I/O system. This approach provides a robust, flexible, and scalable solution for connecting sensors and actuators in harsh environments, simplifying wiring and reducing installation time, and eliminating the need for multiple cables to each I/O module.
Industrial Ethernet is quite common within zoned areas now. Further, based on industrial Ethernet, the Profinet communication standard for factory automation describes the entire data exchange between so-called slaves, such as multiprotocol I/O modules from Turck, and a controller, the Profinet ‘master’.
So, how can this scenario help with addressing a Zone 2 challenge?
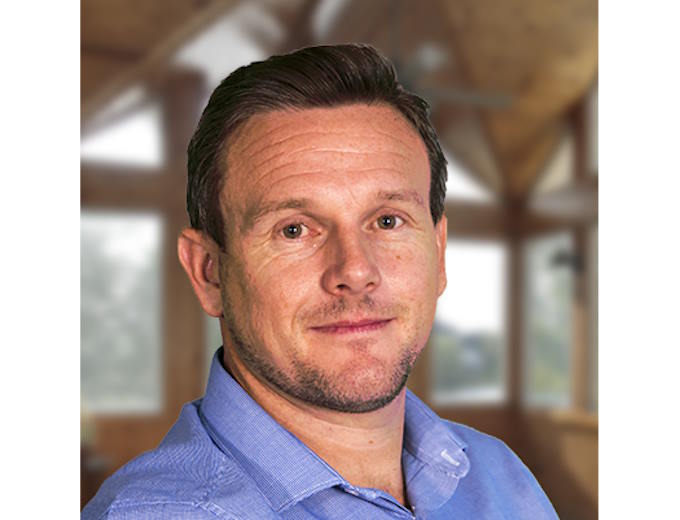
Tony Coghlan, Managing Director, Turck Banner
Zone classifications
Classified as hazardous areas where explosive gases or vapours are not normally present in an explosive concentration, and if they are, it's only for short periods, Zone 2 environments pose several key challenges, especially in industrial environments such as oil and gas, chemical processing, and refineries.
As such, all electrical and electronic equipment used in a Zone 2 setting must be certified as explosion-proof or intrinsically safe according to standards such as ATEX (EU) or IECEx (international). This limits equipment choices and often increases costs.
There are, in fact, three ATEX zones for gas, and three for dust.
Gas Zone 0 has the highest risk level, where an explosive atmosphere is continuously present, or present for long periods (more than 1000 hours per year).
Gas Zone 1 has a moderate risk, where an explosive atmosphere is likely to occur during normal operation (10 to 1000 hours per year).
Gas Zone 2 has the lowest gas risk, where an explosive atmosphere would only occur under abnormal conditions (less than 10 hours per year).
Dust zones are 20, 21 and 22, and have similar definitions to gas, but for an explosive dust cloud.
The “pain” of Zone 2
The reason that Coghlan describes Zone 2 as being potentially painful is that special precautions have to be taken whenever equipment is used, maintained or introduced to a Zone 2 area. This is despite the fact that, for at least 99.9 percent of the time, or 8750 hours per year, the area is perceived as being just like any other non-hazardous area in the factory. Such equipment costs more to purchase and maintain.
While no-one thinks that special precautions in the higher zones are not required, to use an analogy of a domestic kitchen with a situation similar to a Zone 2, would you search for a gas leak in your house with a match?
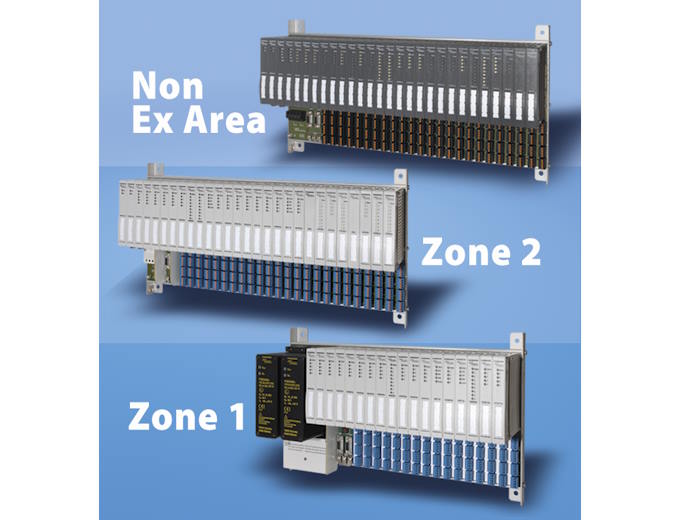
How can we make it less painful?
The best solution would be to change the conditions and remove the risk, so that the area could be declassified. However, as this is rarely possible or practical, what else can we do?
One approach may be to use non-ATEX equipment in a suitable Zone 2 certified enclosure; while this may well reduce the initial cost of the equipment, it is false economy.
The more sensible thing to do, argues Coghlan, is to use products designed for use in Zone 2 which don’t require any enclosure, can be mounted directly to the machine, and which use plug-in connectors everywhere. This can reduce maintenance costs enormously.
The elimination of enclosures makes access far easier, with a gas-free certificate no longer required, to confirm that there is no explosive atmosphere before the cabinet can be opened.
The use of quick disconnect connections ensures that a product can be replaced with no subsequent need for extensive electrical testing. Wiring terminals, as well as being the most common point of failure when replacing any product, also take far longer to repair. Typically, a wiring terminal takes 5–15mins per connection, requires tools (screwdriver, torque wrench, wire strippers, ferrules) and has a high risk of miswiring, loose connections and broken wires. A quick disconnect plug and socket takes between 30s and 2mins per plug, requires no tools and eliminates misconnections.
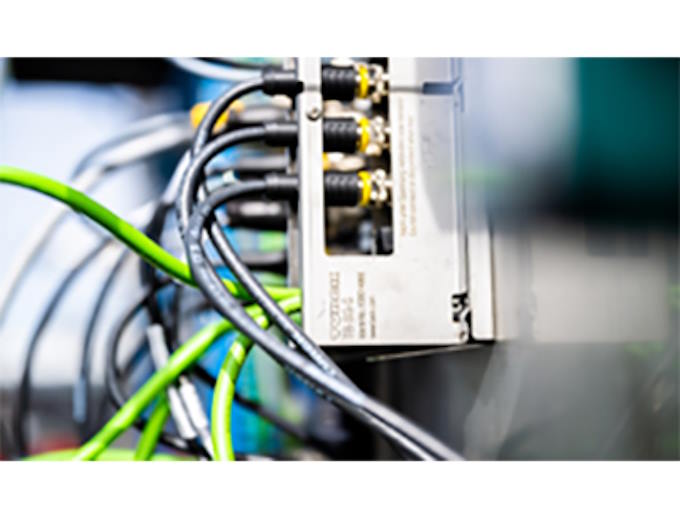
Knowledge and portfolio
Not that it necessarily focuses solely on solutions for challenging environments and situations, such as hydrogen production, but Turck Banner’s portfolio of technologies and products, encapsulated by its breadth and depth of knowledge in such areas, does lend itself (and this isn’t by accident, excuse the pun) to being able to address many of the demands of such hazardous applications.
Its extensive range of products covers all ATEX zones and non-hazardous areas, and can provide everything from the sensor and interconnecting cables, to PLCs and fieldbus products for hazardous areas. Further, Turck Banner’s parent company, Turck, claims to be the market leader in IP67, IP68 and IP69K fieldbus products designed to be mounted directly onto the machine.
Turck also claims to be the only company to produce safety remote I/O modules for Zone2/22, which have a SIL3 rating, and are designed to be mounted directly on the machine where they are needed, with IP65, IP67, IP69K protection class, a working temperature range of -40 to +70°C, CIP safety and Profisafe protocols.
Other relevant products which haven’t been mentioned so far are lighting, indication, wireless I/O, barriers, signal conditioners, RFID in both Zones 1 and 2, and a complete spread of sensors.
Not everyone wants to use field-mounted devices, and Turck Banner appears to be more than capable of supporting every type of installation in all zones. The EXCOM range, for example, is a solution for all zones and non-EX areas, with the ability to hot-swap cards and power supplies even in Zone 1, or bespoke cabinets to the customer’s specifications providing a turnkey approved solution.
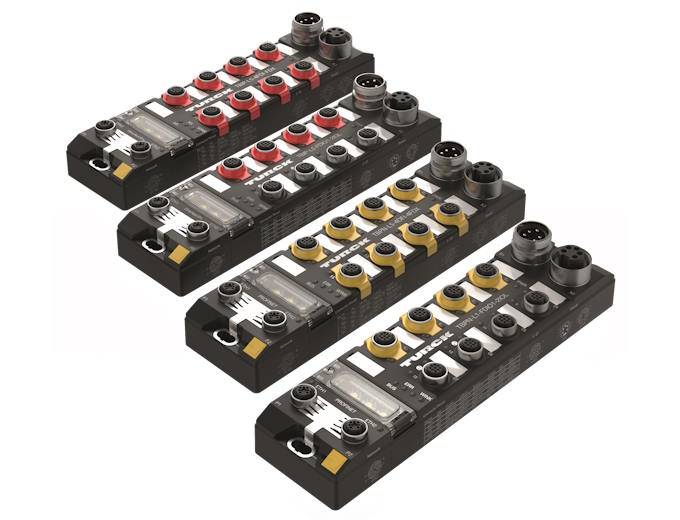
Direct machine mounting
The ability to mount products directly on the machine, close to where they are needed, makes tooling changes simple, or allows for machine modules to be relocated to other production lines as needed.
Mounting directly on the machine can expose the part to more extreme temperatures and physical abuse than would be encountered within a cabinet, so to combat these extremes the products have robust, often metal, housings and wider operating temperature ranges. These include the TBEN range of multiprotocol, digital I/O modules, with ATEX Zone 2/22, cULus, IECEx and CCC approvals, IP65/IP67/IP69K protection class, and a working temperature range of -40 to +70 °C, or the IMC isolating barriers. Turck Banner also provides a bracket for the TBEN and IMC, to ensure that there is no unintentional removal of connections, both fulfilling the requirements of Zone 2 and providing extra protection to the cables.
This environmental robustness is also a huge benefit to companies which supply their equipment worldwide for use anywhere from the tropics to the arctic, and from cleanrooms to quarries or refrigeration units.
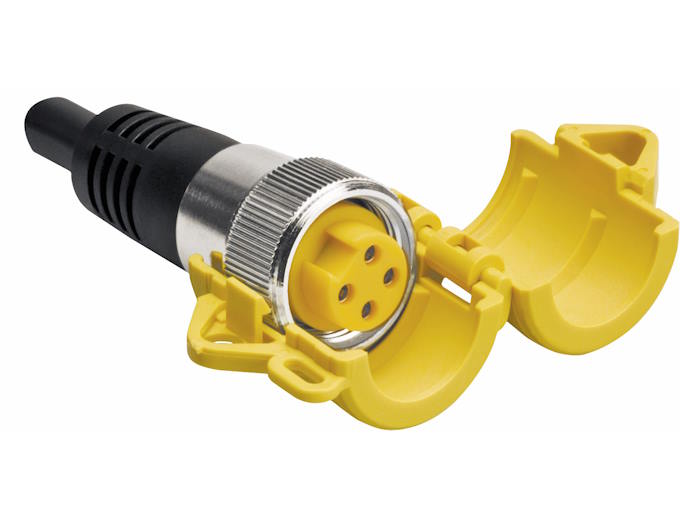
Potential applications
Turck Banner cites skid manufacturing, with its modular, decentralised approach, as one potential application for this approach. Here, equipment may be commissioned off site, which leads to a direct time-to-market benefit. Indeed, any application that involves modular machines, such as aerosol or filling machines, in industries such as food and beverage, could benefit.
From a maintenance viewpoint, there are clear benefits also, with inspection and test simplified greatly.
Conclusion
For those who embrace the Zone 2/22 remote I/O concept, companies such as Turck Banner aim to ease potential pain points with easier maintenance, faster time to market, more flexibility with modular machines, and a reduction in costs over the lifetime of a machine.