Future potential of battery technologies and hydrogen solutions
Author : Tony Coghlan, Turck Banner
02 December 2024
Automation specialists sit in an enviable position of being able to tailor, adapt and apply their software and hardware solutions to evolving applications and sectors, while educating forward-thinking customers about their benefits. They can also create and/or influence certain tech trends, as Turck Banner’s MD Tony Coghlan explains.
In terms of evolving tech solutions, new energy options, such as hydrogen, fall squarely into this equation. How do companies balance the perceived safety concerns against the clear potential of hydrogen as a future mainstream fuel?
The desire to move away from fossil fuels has driven the need for improved battery technology and hydrogen solutions, to replace the petrol or diesel internal combustion engine in all vehicle types.
H2 vs battery
You would need a crystal ball to be able to predict which of these technologies will come out on top. From a consumer point of view, both have their pros and cons. While hydrogen has the advantage of fast re-fuelling, production costs are higher and re-fuelling stations are scarce. Although electric vehicles have lower operating costs, their initial purchase cost is higher, and recharging takes longer. However, the infrastructure for electric vehicles is far more established than hydrogen.
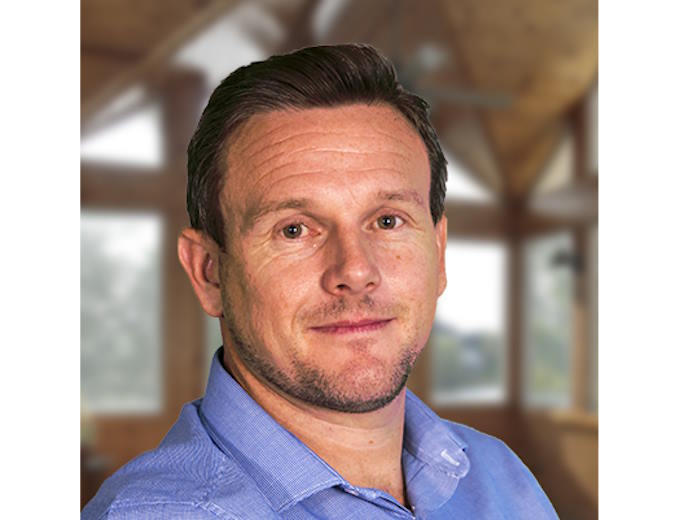
Tony Coghlan, Managing Director, Turck Banner
Safety perception
With hydrogen as a potential future clean energy source, its immediate obstacles would appear to include perceived concerns around its safety, allied to associated challenges with storage, handling and transportation.
A matter of infrastructure
The hydrogen infrastructure will have to be massively expanded in the coming years – be it in the provision of electrolysers and other plants for hydrogen production, pipelines and ships for transport, tanks and other storage technologies, or fuel cells and other plants for using hydrogen.
As with any developing technology, manufacturers have to take steps into the unknown, which can lead to areas of instability in the manufacturing process. To illustrate this point, if a product is well established and has not changed fundamentally in a long time, all of the areas where problems occurred during manufacturing, have already been discovered and dealt with. When a new product line is constructed, all of these problem areas can be avoided.
Another consideration is the temperature range that applies for hydrogen filling stations. Hydrogen needs to be pre-cooled to three temperature categories: T40 (-40 to -33°C), T30 (-33 to -26°C), and T20 (-26 to -17.5°C). T30 and T20 are not used in commercial stations, because they result in long refuelling times. Then, the temperature in the vehicle tank must not rise above 85°C due to the compression of remaining gas. Further, hydrogen is typically stored at 350-700 bar.
For storage, the liquefaction phase can be dangerous due to several hazards, including fire and explosion (hydrogen is highly flammable and can burn quickly and completely in air), frostbite (liquid hydrogen can cause severe frostbite to the skin and eyes), asphyxiation (hydrogen can displace oxygen in the air, making it a simple asphyxiant), cryogenic temperatures (liquid hydrogen is stored at extremely low temperatures, which can cause other gases to solidify and lead to equipment issues), and oxygen enrichment (extremely low temperatures can cause oxygen to condense and solidify, which can increase the likelihood of an explosion). To reduce the risk of these hazards, liquid hydrogen containers are designed with multiple safety features.
Time to market
Another challenge faced by these pioneering manufacturers is time to market, and managing the constant changes brought on by rapid development.
With so much competition in these markets, manufacturers cannot afford the time needed to plan, build, program and test a new production line using traditional methods. In the five-six years that it typically takes to do this, either a competitor has developed an alternative, or their own R&D department has made an improvement.
This time to market can be significantly reduced by using modularity, either as a function of breaking the production line into sections, where each section has independent control and intelligence but is still dependent on individual manufacturer’s products, or by utilising MTP.
The Modular Type Package approach
Modular Type Package (MTP) is a manufacturer-independent interface which describes a module’s functions. The module’s internal control system implements the functions in the same way that a manager delegates a task to an assistant. The higher-level control system doesn’t need to know how the module implements the function, just that it is being done.
The modular approach works because many parts of a manufacturing process are common with other processes. This means that a common section, with its own control and intelligence, can be dropped into the whole line, needing only to interface with the sections up- and down-stream of itself and with the overall control system.
The MTP approach also simplifies the overall control system and programming, and can have the greatest effect on time to market, with a possible reduction of two-three years. Inherently, the faster that manufacturers can adapt their technologies to a potential hydrogen production scenario, the better it would be for future profitability. If solutions may be tested and proven quickly, and uptake is healthy, the better the prospects would be for hydrogen’s prospects as a viable clean fuel.
This modularity also facilitates the ability to incorporate changes during and after construction, where a more traditional approach may have required a complete redesign, or extensive reprogramming. The number of different types of battery cell required to fit all of the different vehicle types demands flexibility in the production line, and modularity is key to achieving this.
From a safety point of view, especially in light of the perceived hazards that hydrogen may present, the decentralised nature of the MTP approach brings clear advantages, both in terms of being able to set up operations off-site, ready for smooth installation and shorter commissioning time, and in terms of being able to implement shut-off easily, when needed.
Condition monitoring
Turck Banner, for example, has all the interface and sensor products required to enable MTP, decentralised automation and local intelligence. It also has an extensive product portfolio for condition-based monitoring.
Areas of instability in manufacturing a new product are not just restricted to new processes. Many moving parts on a production line may be untested or have not had the opportunity for lifetime testing. Data-driven condition monitoring of these moving parts is essential to predict problems before they happen.
The cost of a product and the profitability of a manufacturing process is heavily dependent upon the availability of its manufacturing equipment, the continuous flow of the product throughout the process, and the quality of the final product. Condition monitoring is essential in maintaining the availability of the equipment. Remote monitoring of production flow and quality inspection provides real-time visibility for immediate intervention, and facilitates the tracking of trends in performance, to identify areas where improvements can be made.
Turck Banner’s wireless sensors and networks make it easy for manufacturers to position sensors where needed, to gather the performance data, and also to relocate sensors to pinpoint areas for improvement.
Experience and portfolio
Both Turck and Banner have decades of experience with process automation in explosion-proof areas and every industry sector. Turck, for example, claims to be the only manufacturer who can provide Zone 2 IP67 remote I/O solutions, which can be mounted directly to the outside of a machine without the need for an enclosure. Turck and Banner’s combined portfolio of sensors, safety, lighting, indication, vision, fieldbus, networking, HMI, I/O, connectivity, measurement, interface technology and cloud solutions make them unique in their industry.
An effective toolbox approach, such as that provided by automation specialists such as Turck Banner, can enable integrators to advance future technologies such as hydrogen and EV batteries.
Contact Details and Archive...