This is how future drive technology works
27 September 2018
Control cabinet-free, modular, and flexible – future drive technology will increase productivity along the entire value stream. Bosch Rexroth outline the five requirements for future-proof drive technology – along with the appropriate implementation.
Machines will quickly adapt to new products, production lines can be subsequently expanded, and all that with the smallest possible footprint: The development of cabinet-free drive technology will enable end users to operate more machines in the same amount of space, and offer more flexibility when it comes to adapting existing production facilities to new tasks.
Intelligent servo drives have become an indispensable part of modern machines. They undertake format changeovers or changes to the motion profile at the push of a button. This significantly shortens the changeover times of machines. However, until now the rising number of servo drives has led to increasingly bigger control cabinets.
The more space taken up by “unproductive” control cabinets, the less space available for the actual machines and systems. In addition, industrial companies across almost all sectors are faced with the challenge of increasingly shorter product life cycles. Existing production lines are continuously being adapted to new tasks and supplemented with new processing stations. Consistent modularisation can make these expansions considerably faster and more cost effective.
Below, Bosch Rexroth outline the five requirements for future-proof drive technology – along with the appropriate implementation:
1. No control cabinet – full flexibility
The footprint of machines is a commercial factor that is relevant over their entire service life. Control cabinets take away space from other machines and reduce the available production area.
With conventional drive technology, the motor and control unit are separated from each other. A power and encoder cable runs from each motor into the control cabinet. Machine manufacturers and end users have had to accept this in the past in order to enjoy the advantages of servo technology. Rexroth cabinet-free drive technology retains all the advantages of servo drives and combines them with up to 90 percent lower cabling costs and a significant gain in space by eliminating control cabinets.
Back in 2007, Rexroth presented the world’s first motor-integrated servo drive, the IndraDrive Mi. In 2014, the manufacturer reached a new milestone with cabinet-free drive technology. Since then, all network access components previously located in the control cabinet have been designed according to IP65 and can be installed directly in the machine. The mains module is a single unit containing the mains filter, the mains choke, and the mains contactor, and is connected directly to the mains. The regenerative supply module with control electronics, braking resistor, and braking transistor completely replaces the supply and control electronics in the control cabinet. This allows the control cabinet to be totally eliminated. End users gain valuable space for additional machines in their available area.
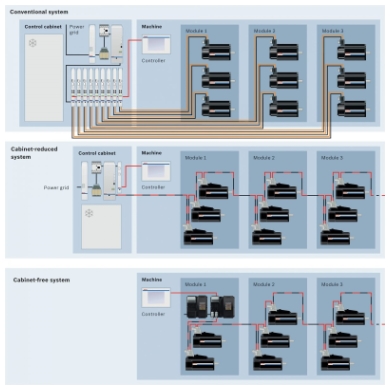
No control cabinet – full flexibility
Up to 30 servo drives form a drive system on a cable harness of up to 200 metres long. Only the first drive is connected to the power supply and control by a cable, and from then on all other drives are connected in series using a hybrid cable for power and communication.
Compared to traditional automation, this approach reduces the cabling by up to 90 percent. A conventional control cabinet solution with ten drives will typically require 110 metres of power and encoder cables. Cabinet-free drive technology reduces this amount to just 10 metres of hybrid cable with the same motor spacing. This not only cuts material costs and installation times, it also reduces the probability of faults in the cabling. However, the savings are actually even higher because sensors, I/Os, and field bus components can be connected directly to the decentralised drives.
2. Modularity in electronics – easy combination and expansion
Production lines have to be adapted to new products and processes more quickly than ever before. The subsequent expansion needs to be easier and faster than previously possible.
Cabinet-free drive technology opens up new possibilities for modularisation and also makes it easier to incorporate stations into existing production lines at a later date. Until now, expanding a production line often led to long stoppages. The fitters had to install each drive individually in the control cabinet and wire it to the motors. While this is being done, the line cannot produce for safety reasons. The drives are then commissioned on site, which in turn requires time.
By contrast, cabinet-free drive technology enables machine manufacturers to pre-install the corresponding modules and commission the drives in their plant. These modules can be combined according to the end customer’s requirements. For the integration into existing lines, all that has to be done is to set up the power supply and connect to the higher-level control. Commissioning costs are significantly reduced as the drives are already parameterised. This reduces machine downtimes for converting the line to a minimum.
Some machine manufacturers have already implemented this approach to using cabinet-free machines. The packaging machine manufacturer Gerhard Schubert GmbH from Crailsheim presented the world’s first cabinet-free packaging machine, which is based on the IndraDrive Mi drive system, at interpack 2014. It consists of several robot modules, an operator control system, an integrated image processing system, and the flexible Transmodul transport system. This enables the company to construct flexible and modular machines to perform all packaging tasks, such as feeding, filling, sealing, labelling, and palletising.
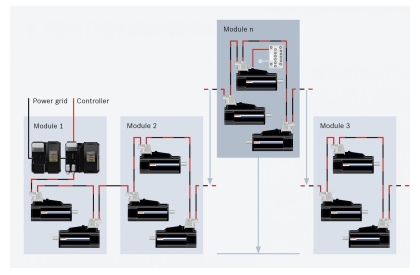
Modularity in electronics – easy combination and expansion
“The Rexroth drives allow us to completely eliminate conventional control cabinets”, says Managing Director, Ralf Schubert. “Customers were so impressed with the machine, we have been designing all our machines without a control cabinet since 2016.”
One of the key advantages of the IndraDrive Mi is that the multi-Ethernet interface supports all standard Ethernet protocols including Sercos, PROFINET, EtherNet/IP, EtherCAT, and POWERLINK. A gateway can also be used to connect to Profibus. As a result, the modules can be incorporated into the end user’s automation landscape with no additional costs. A further advantage is that the multi-Ethernet interface minimises the variant diversity and thus reduces inventories in maintenance.
3. Safety guaranteed at all times
Standard-compliant machine safety is a fundamental requirement. Fast restart after manual interventions increases the availability of machines and production lines.
A key prerequisite for cabinet-free drive technology is machine safety. End users expect the same integrated safety functions as on drives whose controllers are housed in the control cabinet. On the one hand, this involves implementing the specifications for functional safety in accordance with the standards. On the other hand, however, they also expect maximum machine availability, i.e. that the machine operates productively again as quickly as possible after a manual intervention.
Decentralised concepts simplify the implementation of the Machinery Directive thanks to modularisation. Rexroth also provides certified safety functions in the cabinet-free IndraDrive Mi. The hybrid cable transmits all safety signals. As a result, separate wiring is no longer required. This reduces both cabling costs and the possibility of faults in the wiring.
A particularly important feature is the easy implementation of safety zones with multiple drives on a single drive train. For Safe Torque Off, the first drive in a safety zone is wired in such a way that it processes the safety signals. To add further drives to a safety zone, it is sufficient to use a safety subscriber connector. This makes commissioning extremely easy and ensures transparent operation.
Multiple safety zones are possible in a single drive train. This solution reduces the time required for restarting after a manual intervention and thus increases the availability of the machine. In addition, SafeMotion provides extensive safety functions – from safe stop through to safe movements. Functions that do not require an encoder, e.g. SS1, SS1-ES and STO, are certified with Cat. 4 PL e in compliance with EN ISO 13849-1 and SIL 3 in compliance with EN 62061. Functions that require encoder feedback, e.g. SS2, SOS, SLS, SMS, SMD, SLI, and SDI, are certified with Cat. 3 PL d in compliance with EN ISO 13849-1 and SIL 2 in compliance with EN 62061.
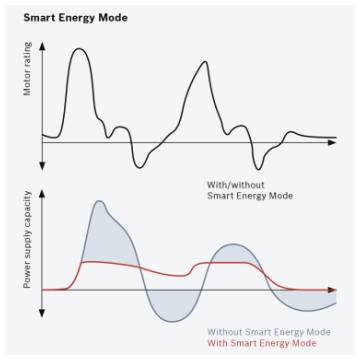
Efficient use of energy
As a protocol, IndraDrive Mi uses the CIP safety standards Safety on Sercos (CSoS) and Safety over EtherCAT (FSoE), as well as PROFIsafe on PROFINET. The signals are simply transmitted with the standard data. The integration of drive, peripherals, safety buses, and standard Ethernet communication in a single network simplifies handling and reduces hardware and installation costs.
4. Efficient use of energy
Greater energy efficiency has a direct impact on operating costs. Modern drive solutions reduce power consumption and lower the peak loads.
For many end users, one of their key specifications is for their machines and systems to achieve higher energy efficiency. On the one hand, this enables them to contribute to environmental protection, while on the other hand, energy consumption determines a significant proportion of machine life cycle costs.
Cabinet-free drives provide an effective lever in this area. Thanks to the system-related energetic coupling via the shared hybrid cable, energy can be exchanged between the drives. For example, if one drive brakes, the resulting braking energy can simultaneously be provided to an accelerating drive in the machine. The energy is thus retained within the system or, if too much energy is generated, fed back into the network. This allows energy savings of up to 50 percent.
In addition, there is no power loss in the control cabinet. In conventional drive systems, this can sometimes produce high temperatures in the control cabinet, which makes cooling necessary. With cabinet-free drive technology, the hardware costs for control cabinet cooling are eliminated in most cases. In turn, this eliminates the energy required for the cooling, further increasing energy efficiency.
In addition, the supply module is designed for a broad voltage range, allowing it to be used worldwide for mains voltages from 380 V to 500 V. It generates a regulated DC link voltage for the individual drives. This ensures that a machine always achieves the same performance on all mains voltages. Thanks to its regulation, the device is resistant to mains voltage fluctuations.
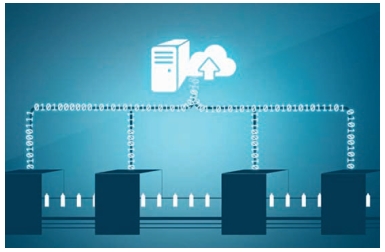
Networking has begun
However, active regulation of the supply module brings additional advantages. System perturbations are reduced to a minimum, making additional measures superfluous. Integrated reactive current regulation not only compensates for internal reactive current requirements, it also provides compensation for other inductive or capacitive consumers. The losses caused by the reactive current are thus completely eliminated. Thanks to its intelligent regulation, the Smart Energy Mode ensures that optimum use is made of the energy stored in the DC link due to the system principle. As well as limiting power peaks, it also reduces the average energy consumption. In practice, this results in reductions of up to 60 percent in power peaks, and cuts the average power by up to 30 percent. As all mains supply components are designed for the average power, it may be possible for these components to be made smaller in some circumstances.
5. Networking has begun
All Industry 4.0 concepts require decentralised intelligence and high connectivity of automation components. Future-proof solutions from the Connected Automation portfolio support all standard Ethernet-based real time protocols and are open for communication with higher IT levels.
One requirement that will be increasingly important in the future is the ability to network vertically with the company’s IT, in order to implement Industry 4.0 approaches. The objective is direct access to the drive by IT functions. Servo drives have decentralised intelligence and perform their tasks autonomously based on specifications from higher levels. Equally important is that their multi-Ethernet interface means they already support both horizontal and vertical networking, and are set up for comprehensive data exchange.
In addition to all the possibilities provided by PLC-based automation in compliance with IEC 61131-3 and PLC open, as well as OPC UA technology, Rexroth is the first drive and control manufacturer to create a bridge between drive technology and the world of IT with its Connected Automation portfolio. The Open Core Interface for Drives interface technology integrated into Open Core Engineering allows direct access to all drive parameters using high-level language based applications on external devices such as PCs. Instead of independently created PLC programming, for example, macros in standard spreadsheet programs are sufficient to directly retrieve and evaluate drive data such as energy consumption. With self-programmed apps for popular smartphones and tablet PCs, machine manufacturers are already simplifying the commissioning, parameterisation, and diagnostics of the intelligent, decentralised drives from Rexroth.
Summary: Cabinet-free drive technology is future-proof
Cabinet-free drive technology meets numerous requirements from machine manufacturers and end users for which they previously had to accept compromises. Now, they can use more servo drives without reducing their productive area due to the increasingly bigger control cabinets. The opportunities provided by complete modularisation reduce the effort and costs involved in the subsequent expansion of existing production lines. Standard-compliant safety at the drive level with a smart solution for the easy switching of safety zones increases machine availability. The simple energy exchange within the drive system reduces the average power consumption and limits power peaks. With the multi-Ethernet interface and its own intelligence, Rexroth’s cabinet-free drive technology can also be incorporated into future Industry 4.0 environments.
Contact Details and Archive...