Preparing Manufacturing Systems for Industry 4.0
05 March 2019
Industry 4.0 is set to revolutionise manufacturing and the benefits it offers will redefine production efficiency and quality levels. Merging real and virtual worlds and enabling technologies such as 3D printing, Cloud computing, Big Data and the Internet of Things; Industry 4.0 presents manufacturers with a new world of opportunities for their businesses – but do they have the plant floor software to realise the bounties on offer?
This article will look at what Industry 4.0 means to manufacturers, how it will impact the way in which they operate and what it means for plant floor IT systems.
What is Industry 4.0?
Industry 4.0 will disrupt our current understanding of manufacturing systems and is focused on gaining real and measurable business benefits. It has gained such recognition, funding and acceptance as the path to the future because it offers such a compelling business case. Its philosophy has the potential to increase business agility, enable individual customer requirements to be met, lower production costs; enhance product quality and increase production efficiency. It is based on Cyber-physical Systems (CPS) and Cyber-physical Production Systems (CPPS) and embraces the latest technology innovations such as Cloud computing and the Internet of Things. While it offers enormous, new opportunities for businesses; the scale of its impact also brings new challenges.
Developed as a public-private endeavour in Germany, Industry 4.0 is widely accepted across Europe and China and is similar in many ways to the Smart Manufacturing initiative in the USA. It is the vision of the fourth industrial revolution. Beyond embracing new technology enablers, it differs from previous revolutions in two major ways:
1. It has been predicted and so companies can plan for it.
2. It not only re-defines levels of manufacturing efficiency and productivity; it opens up entirely new business and revenue stream opportunities.
Having been given this vision of the future, manufacturers can now plan their transformation. The Industry 4.0 model gives a vision that uses CPS and CPPS to provide a pathway for enabling technologies to produce ‘smart’ results in terms of innovation, services, supply chain and manufacturing.
Bringing together intelligent systems and data in a completely connected environment means that supply chains will become highly integrated and transparent. The mapping of physical flows through a plant and beyond gives an end-to-end track and trace capability that can improve supply chain reliability and agility. The Smart supply chain will also enable online marketplaces and bidding to further streamline processes and drive costs down.
Technology enablers
A swathe of new technologies has been introduced over the past decade. They offer new capabilities and, together, present a new environment that manufacturers can use both inside and outside of their plants. They impact on manufacturing costs, quality, data and agility, and these innovations underpin the Industry 4.0 model:
Embedded electronics – The miniaturisation and reduced cost of electronic components allow them to be included within many products. The capabilities that electronics encompass are quite diversified:
a. Tags and sensors, such as RFID which enables comprehensive tracking across plants and throughout supply chain.
b. Embedded communication – Internet everywhere opens up new possibilities in coordinating across devices and products. Embedded communication is one of the foundations for the Internet of Things and machine-to-machine connectivity.
c. Embedded computing – The reduction in cost and size of microcontrollers and other computers means they can now be added to more products. Embedding computing capability gives us smart products, smart equipment and a level of intelligence that enables processes to run with little or no operator intervention.
d. Embedded actuators – The highest level of CPS is achieved when products or equipment not only have sensors, but also actuators allowing automatic transformation of their behaviour and even physical characteristics
Mobility – Adding intelligence, sensors and bi-directional communication capability to devices means they can be connected to systems from anywhere. This gives geographic flexibility and connects products as they move both through the plant and through the supply chain.
Cloud computing – Adding sensors, processing and connectivity capability to more things generates masses of data from many locations. Cloud computing gives us both the storage and the ‘anytime, anywhere’ ability to handle this data – making it freely available for the advanced analytics required by Industry 4.0.
Advanced analytics – Simply collecting a lot of data doesn’t create new levels of manufacturing efficiency. Advanced analytical software can transform masses of structured and unstructured data into intelligent, structured information. Such powerful software with huge volumes of data to feed from also means it can be used to help predict scenarios for even more effective production strategies and decision making.
3D printing – This technology has revolutionised prototyping, enabling much faster, lower cost models to be produced and increasing the efficiency of a new product introduction. It can also be used to create parts and entire multi-material products.
Using 3D printing removes the necessity for other discrete, complex, costly machines and can streamline production processes with great benefit.
Community platforms – In the same way we share information with friends on social media, businesses are now also seeing the benefit of community platforms. They enable collaboration without the limits of geography and can help with solving problems, finding information more quickly and generally enhancing global learning and improvement.
CPS and CPPS
Cyber-physical Systems integrate computational networks with the surrounding physical world and its processes. Using the masses of data being generated and data processing services available on the Internet, they offer opportunities for enhancing a wide range of environments from traffic management through to health care. In the manufacturing environment, Cyber-physical Production Systems enable software-enhanced machines to leverage the wide range of data from sensors and actuators. They incorporate self-management capabilities; know their own state, capacity and configuration options, and are able to make production decisions without operator intervention. This offers the manufacturing world a revolution where de-centralised systems provide a new way of operating that gives benefits such as robustness, autonomy, self-organisation, self-maintenance, self-repair, predictability, new levels of efficiency and interoperability as well as global tracking and tracing.
A CPS contains the smart materials and products in a plant. These act as service consumers. A CPPS holds the smart plant and its equipment. This is the service provider. While not physically coupled, the two sets of systems request and respond to the needs of materials to be processed.
The vision for the future
Industry 4.0 offers overwhelming benefits. The levels of automation it will bring with it mean that fewer people will be needed to operate a plant and that day to day costs will be much lower. Automated decision making will further mean faster responses and much greater efficiency. The agility Industry 4.0 offers will mean plants will be able to handle a much more diverse product range with shorter lead times. The ability to quickly customise orders to specific requirements and even to build one-off specials economically will give a much higher responsiveness to customers’ needs and enhance their overall experience.
The intelligent operation and data analysis within the Industry 4.0 plant will give complete visibility of an operation; enabling smarter strategic decisions and further enhancement to processes. New products will be able to be created, tested and introduced at a much faster rate, further facilitating market innovation and breakthrough technologies. Assured quality, consistency and reliability will further add to the value of products. Overall this revolution will enlarge markets, increase profits and help to improve customer service in such a way that will promote high levels of customer loyalty.
Manufacturing Execution Systems (MES) for Industry 4.0
Over recent years, MES (or Manufacturing Operations Management (MOM)) have been vital to the success of global manufacturing operations; enabling performance, quality and agility goals to be achieved. What then will happen to these systems with the dawn of Industry 4.0?
MES already work in real time; handling rapidly flowing streams of disparate data and turning it into useful information. They provide critical information for the production environment, supply chain, customer service, product development and plant management team. The Industry 4.0 concept will continue to evolve and grow as further technology enablers and innovations are created to support it will be a process It will not be implemented overnight and will require a roadmap and staged introduction over time, with plants focusing on priority areas that offer fastest and greatest benefits. MES will play a vital role in this process as they give manufacturers a foundation around which they can build an Industry 4.0 structure for the future.
Of course MES cannot stand still and the traditional systems need to advance if they are to help in meeting the vision for the future. Most MES on the market today can manage a current factory but these systems need to evolve to handle the new challenges created by the Industry 4.0 structure. These challenges are grouped in six main categories as follows:
Challenge #1 - MES and the Internet of things
The Industrial Internet of Things (IIoT) will first of all democratise equipment automation. Until now only sophisticated equipment, usually in advanced manufacturing environments, would allow its automation via more or less sophisticated interfaces. Through these interfaces software applications could read engineering process, product or equipment variables and could also act on the equipment (e.g. make it stop or run, or download the recipe to be used). With IIoT, however, even legacy equipment without any interfaces can allow automation – e.g. placing sensors by the equipment allow collecting info such as temperature readings, number of pieces produced, equipment status, etc. However, IIoT in I4.0 goes way beyond the possibility to automate legacy equipment. In fact, on a shop floor, there are multiple opportunities to leverage the power of connected things. As electronics for sensors and actuators with computing and communication power become affordable and extremely small, these can be attached to literally anything in the shop-floor: equipment, products, containers, consumables, durables, spare parts, etc.
There are quite significant amounts of challenges in IoT related to hardware, low level embedded software, communication protocols and security, but none of these concerns directly affect manufacturing execution systems or manufacturing operation management software. In fact, MES/MOM must be abstracted from these low level details. It is a consumer of lower-level services and will therefore benefit from the great evolution this area is having due to all the work many researchers and companies are devoting to the topic.
The role of MES in IoT starts then at a higher level and in two areas. First there is the context area. There is sometimes a misperception where IoT will directly connect to the cloud so that its values can be used in Big Data analytics – but this is not likely to be the case. First, data collected from sensors is probably useless without the appropriate shop-floor context that MES provides. Say a data temperature of a sensor – MES shall provide info on the equipment it belongs to, what the settings of the equipment were, which material was being processed, etc. so that the information the sensor collects can be useful.
Secondly there is the orchestration area. Most of the time devices are somehow connected and have capabilities that can be used to automate manufacturing processes or workflows. The question is how to get them to be “universally” connected and exploit that connection in a business meaningful way.
The orchestration must then deal with aspects like:
-Once an IoT-enabled element becomes available, how does it register to become available to be orchestrated at the MES level?
-When it is available to be orchestrated, how will the right MES context be added to the readings?
-Once the context is available, how is it decided that these values are all being sent to big data structures and/or stored locally and/or be associated with materials (e.g. in engineering data collections) and stored in the MES?
-How can the IoT be instructed to collect a reading every x seconds?
-How can the orchestration with other agents or applications be configured?
So what is needed at the MES level is an agent which is capable of configuring the expected behaviour of the IoT and its integration in the shop-floor area or above.
Challenge #2 - MES logically decentralized system
The dynamics of shop-floor operations with smart materials and smart products are probably one of the biggest challenges for MES systems. As an example, a smart product CPS knows its state, its position, its history, its target product and its flow alternatives. Likewise, a smart resource or CPPS will know its state, its history, its maintenance plan, its capacity, its range of possible configurations and setups, etc.
Therefore, on one side we have one-off or unique materials; making it very difficult to centrally optimise shop-floor operations in a classical way. On the other, the elements involved in shop-floor operations have sufficient intelligence to become autonomous. The logical consequence is that the shop-floor will become a marketplace acting as a decentralised system with intelligence in independent entities.
Smart materials and products (CPS) are service consumers and smart equipment and plants (CPPS) are service providers. CPS and CPPS are not physically coupled; rather, a dispatching operation delivering logical binding between a material to be processed and a resource to process the material.
What this means is that a smart product or CPS has the capability to identify itself, providing its position and state to a physically centralised system. MES decentralisation needs to be logical, not necessarily physical. In fact, with cloud computing, it’s even arguable whether such a system can be considered physically centralised. What is critical is that the logical decentralisation must exist.
In the marketplace logic, the CPS or smart material knows from the beginning of its existence what it needs to be produced. So it will ask the different possible equipment, the CPPS, for the price of a given operation. Depending on the capability, availability and efficiency, each piece of equipment will bid for performing that operation and the smart material will then chose the cheapest operation. The CPS will then transfer the recipe to the CPPS so that it can perform its unique transformation process.
Although this is shown for only one operation, the smart material needs to optimise not just one processing step but the entire sequence of steps in order to get its most optimised flow – although it will be able to dynamically recalculate the best options upon each new processing step to be performed.
So this future operating model is like having no centralised MES system. Instead, each entity has its own mini-MES which is capable of performing all necessary calculations, optimisations and decisions. However, practical reasons of consistency, maintainability, integration with the factory processes, etc. lead us to conclude the best possible system is one that implements a logical decentralisation instead of a physical one. So the decentralised system with each entity having its digital twin with decision autonomy is mapped in a physically centralised system.
This dynamic marketplace of CPS and CPPS still has many consequences and challenges for the MES systems. First, rather than holding a single unifying model, the MES needs context resolution possibilities. This allows a product that requires a certain service at a certain step to combine the flow of its product category to be adapted, or unique to its specific context. Second, the MES needs to be composed by entities or objects that are completely decoupled, with an external service being responsible for the coupling. Third, because factories will not become full of CPS and CPPS overnight, the MES must provide a system which allows both classical models of allocation (based on traditional scheduling or dispatching optimisation) and the dynamic models of marketplace. This will allow manufacturers to have the basis to migrate their business model without systems that hinder this transition.
Challenge #3 - Vertical Integration
The vertical integration has always been one of the most important aspects in a Manufacturing Execution System, but the Industry 4.0 concept brings the importance of this topic into a completely new level of magnitude.
It is important to note that MES need to map both the physical flows of the factory and the logical/business flows; the latter being equally or even more important than the first. The days of MES doing simple registration for report or traceability of lots and equipment are long gone. Although the MES name has been mostly maintained despite efforts to call it MOM - Manufacturing Operations Management, today these applications cover a wide range of areas.
MES has always been most effective when integrated into the ERP systems ‘above’ it as well as the monitoring, control and actual production processes ‘below’ it. This vertical integration is an enabler for the orchestration of business processes that may be simple or complex but nearly always require multiple layers and groups to be involved. Business processes for compliance, quality, logistics, engineering, sales or operations all have components inside the plant as well as others that reside beyond the factory that are crucial to a business process being executed effectively. Without these, it’s almost impossible to properly manage a production floor of a certain complexity.
It is therefore of utmost importance to consider that with cyber-physical systems being autonomous and communicating directly, the manufacturing processes must not be avoided. This is actually another extremely good argument for the logical instead of physical decentralisation. So in practice, while CPS and CPPS communicate “directly”, the system must trigger business rules or workflows. It can be seen as an interoperability aspect, but with special considerations.
As an example, imagine a case where a smart material autonomously decides to be processed by a given smart equipment and immediately start processing. However, a quality business rule demands that such a lot needs to undergo additional verification steps which are determined by a higher level sampling plan. It is essential therefore that the bidirectional communication somehow intersects the business rules, so that a given workflow is followed before allowing the product to take its planned course.
In another example, a CPS or smart product may know that it needs to collect a measurement variable. The layer above then specifies and checks whether the outcome is correct. This is where statistical process control (SPC) rules reside and, if it’s not within limits, it might open a corrective and preventive action (CAPA). All of that activity will be in a layer above the CPS as it requires data collected over time from other smart materials.
Vertical integration needs to also consider the data stratification and filtering/sampling along the different layers. While a CPS may produce significant amounts of data that can be locally stored for some time and could be sent to big data structures, only some of these values are actually relevant to the required shop-floor levels above, e.g. a few samples that are maybe stored at the MES material level. While this is not really new for manufacturing facilities with automation layers and data collection from available equipment interfaces, it gains a completely new dimension with IIoT.
So, within the plant, the MES will need to aggregate data and put these additional data flows into context. Vertical integration of these autonomous entities is critical as they could otherwise make decisions independent of the rules and best practices for the factory or company. MES providers must continue to expand the product capabilities to ensure that all plant activities are visible, coordinated, managed and accurately measured. Only then can the enterprise systems respond effectively.
Challenge #4 - Horizontal Integration
Horizontal integration at the shop-floor level requires service-oriented ways of alerting the rest of the information system to the information available. However, that is not likely to all come from the CPS and CPPS directly. In Industry 4.0 the MES solution must be truly modular and interoperable so that all functions or services can be consumed by CPS smart materials, CPPS smart equipment or any other shop-floor entity. As an example, a typical maintenance management process, often centralized, could consist of a series of services that each piece of equipment might use.
But the concepts of shop-floor marketplaces for unique products are not only true within a specific factory but also along the complete supply chain. When a particular product is requested by the end customer, different manufacturing facilities and even processes within these facilities will compete in a big marketplace. The necessary coordination and transparency is ensured in I4.0 by a logical entity called supply chain tower.
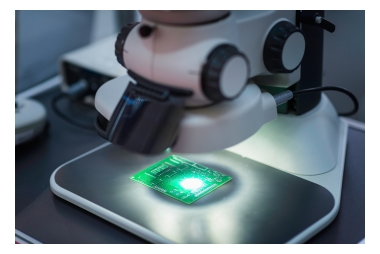
This overall marketplace approach goes beyond what was already present in some MES where integration would already extend from the plant systems of suppliers to connect into the plant systems of their customers. Particularly relevant in this context is the necessary support for the Manufacturing as a Service model (MaaS). In this model facilities no longer compete only for using their entire process to create a complete product or sub-product, but instead make available individual equipment or process to be consumed in single steps. So the MES must support all of this with extreme flexibility, exposing all its available high-granular services as well as its capacity and future plans.
Obviously this complete supply chain visibility and exposure brings significant security and IP related challenges which also need to be properly supported by the MES with multi-dimensional security (at a service level but also at individual process, step and equipment levels and at any combination of these). In the Industry 4.0 final report, horizontal integration focuses on supply chain status communication among facilities and trading partners. Horizontal integration enables the smart supply chain or network to be transparent so status is always visible.
Challenge #5 - Mobile, Virtual and Augmented Reality
Advanced manufacturing environments have had highly integrated connectivity for a long time. As an example, some of the more sophisticated semiconductor facilities have RFID transponders in the material containers. Equipment has bidirectional communication through interfaces which expose readings from sensors, alarms or reports and which allow recipes to be externally selected or downloaded. Industry 4.0 is now creating a true democratization of such connectivity, allowing it to be widespread in manufacturing facilities of different sophistication levels.
Visualisation and control with such spread and autonomous elements, however, will become a huge challenge which cannot continue to be handled by standard, fixed, desktop-like workstations. Fortunately mobile devices have evolved so quickly that they are a quite viable alternative to these demanding tasks. Although the Bring Your Own Device (BYOD) movement is still far from being widely adopted due to security and distraction concerns, it is already well accepted that more controlled mobile devices truly decrease operational costs and offer significant potential for productivity increase.
Some usage types are more obvious than others in business-case terms, for example maintenance technicians. It is extremely inconvenient for them to jump from equipment to equipment when executing planned or unplanned maintenance activities, having to login in nearby workstations to register the activities performed or for instance request spare parts. But this will be a reality in many other areas and roles. The decrease in operational costs, both direct (through cheaper equipment) and indirect (clean-room physical space or time-spent to move and login into the stations) will almost always represent a tangible gain.
With all the amount of data sent by sensors, products and equipment it will also be possible to visualise in real-time the complete status of a production floor using 3D maps. With this data and the availability of mobile devices, virtual reality (VR) will quickly become mainstream. This in turn opens the door to completely new scenarios, such as the use of sensors incorporated in the smartphone or tablet. Some of these are more or less obvious such as using the built-in camera to identify equipment, products, containers or materials. Some Augmented Reality (AR) scenarios, however, are really compelling and will become more so as the different manufacturing physical entities are mapped into the digital-twin via IIoT and visualised in the MES. The key aspect is to identify where someone is inside the manufacturing facility, in which direction they are facing or directly communicating with an IoT-enabled manufacturing element.
Some challenges are not yet fully resolved. As there is no GPS inside the facilities, some other location technologies must be used. This could include indoor positioning using Wi-Fi triangulation. Then, using the built-in gyroscope, one can know exactly where someone is and what they are seeing. Other alternative or complementary techniques include image pattern recognition from the built-in camera.
This leads to several scenarios where this can be used inside a facility. Three quick examples:
Pointing the device at a certain piece of equipment and, upon positive identification, additional virtual data can be added to the screen. This data could be the current status of the equipment; which material is being produced; some important KPI’s, e.g. OEE; live streaming data of an online measurement (e.g. coming from an IoT-enabled temperature sensor); historical information about that equipment, such as when the last maintenance activity was performed; planned scheduling; etc.
In specific operations related to a piece of equipment, an app may add important information for the operation being performed. Parts that a maintenance technician is supposed to check or replace as part of planned activity may be highlighted or gauges or the consumables level for an operator to check as part of a normal work instruction may be emphasized on a display. When searching for a specific product or material, say for logistics or for quality inspection, an app may use arrows added to the camera image to guide the person throughout the facility until reaching the product or material which is also highlighted for a quick identification.
Despite all the futuristic aspects involved, MES with support for mobile, VR and AR have all the conditions to become one of the fastest Industry 4.0 visions to materialise.
Challenge #6 Could and Advanced Analytics
The Smart Factory vision of Industry 4.0 requires achieving a holistic view of manufacturing operations. Clearly this can only happen by integrating data from several different sources rapidly and flexibly. This suggests the MES of the future must also leverage cloud computing and advanced analytics.
Cloud computing is the obvious infrastructure for the speed and agility suggested by Industry 4.0. On-premises systems have far more limited ability to expand, change and respond, and would result in undue costs. Manufacturing data analysis is an area where some leading manufacturers are already starting to leverage the cloud.
Despite the obvious advantages and the additional impulse provided by IIoT, however, cloud-based systems are struggling to become a reality, particularly in advanced manufacturing environments. What may seem a contradiction has to do with the natural risk-adverse nature of bigger corporations based on three issues:
First, a technical issue related to the real-time integration of IIoT. The amount and frequency of data make it very challenging for cloud based solutions to cope with, particularly in what network latency is concerned.
The second issue always present is the dependency on internet providers. Despite the evolution over the recent years, high-investment factories require their assets to operate 100 percent of the time. Any stoppage of systems which production depends on has unacceptable costs.
Third is IP related. Particularly relevant in advanced manufacturing environments where IP may well be the biggest asset a company possesses, there can be no compromise. While once again there has been a tremendous evolution is terms of security, there are always publicly visible incidents which raise the concerns over security in public clouds.
Sooner or later, however, the pure, classical, on-premises MES installations will be the exception rather than the rule. The advantages of using the Cloud are compelling and many different cloud solutions are popping up, such as private and hybrid clouds.
In terms of data, while many MES have manufacturing intelligence components today, these must expand to better accommodate the diversity and volume of big data. Both CPS and CPPS will generate huge amounts of data, which needs to be stored and processed. Advanced analytics are then needed to fully understand the performance of the manufacturing processes, quality of products and supply chain optimisation. Analytics will also help by identifying inefficiencies based on historical data and pointing staff to corrective or preventive actions for those areas.
So future MES must accommodate both offline and real-time analyses. In “real-time” analysis, reaction speed is key as it prevents errors from occurring or being repeated. It is therefore paramount to trigger actions in the plant as quickly as possible, even before data is stored. This needs techniques such as “in-memory” and complex event processing. Depending on the value of products being produced, this ultra-fast response is able to drive very tangible gains.
Another area quickly gaining increased importance is the advanced offline analysis using very sophisticated statistical process models. These will need to be both in structured data, generally residing in a relational database or in data warehouse cubes, and in unstructured data, which is very difficult to analyse with traditional tools. Particularly driven by IoT, as the number of data sources increase and each one can produce up to thousands of data points per second, this will soon be one of the most important aspects to consider.
MES systems do not necessarily have to incorporate their own big data solutions. They must, however, allow a flexible and continuous export of data from the relational databases into flat data models of big data and they must create mechanisms to allow manual or automatic actuation upon the results of the big data analytics.
Future-ready MES
MES are control systems that enforce engineering standards and manage and monitor the work in progress on the shop floor. They are expected to continue to play an essential role in manufacturing as part of the Industry 4.0 vision. However, as is made clear above, the traditional user-interface focused MES will no longer be effective.
Future-ready MES need to be scalable and able to coordinate autonomous, decentralised and dynamic activity. As well as the traditional functionality in handling operations, MES will need to be able to offer the levels of connectivity, mobile application and advanced analytics that are an inherent part of the Industry 4.0 vision. They need to coordinate activities beyond the shop floor and across the supply chain; giving updates on production information from any location, partner or CPS that requires complete vertical and horizontal integration with a constant flow of data. They require the flexibility to handle one-off or custom products in line with individual customer needs which necessitates processing logic beyond repeatable actions and simplistic engineering standards.
Summary
MES are an important part in the development of Industry 4.0 plant floor environments. Traditional MES platforms have been pivotal in successful, modern manufacturing plants. They have offered control of operations to ensure smooth running of the plant floor. However, Industry 4.0 requires a new breed of MES that embraces the flexibility, agility, intelligence and connectivity of the Smart Factory. To meet these needs, the way an MES operates needs to change to accept a comprehensive, decentralised way of operating throughout the plant and beyond. This requires new levels of connectivity and new ways of approaching how users interface with equipment.
Industry 4.0 is a revolution that will come but it will not happen overnight. Traditional MES cannot be twisted to fit this new structure. Such systems need to evolve to embrace the fundamentally different way of operating a highly intelligent plant floor with de-centralised control. Manufacturers need to understand the differences between traditional and future-ready MES if they are to use this important platform as a pathway to reaping the huge benefits Industry 4.0 has to offer.
Contact Details and Archive...