Why manufacturing IIoT projects are failing
07 December 2020
The Industrial Internet of Things (IIoT) has promised much, but why are manufacturers struggling to successfully adopt the technology?
The IIoT is one of the core technologies for Industry 4.0 (I4.0), offering a way to gather huge volumes of ‘Big Data’ from throughout the shop floor and beyond. The intelligence within this data offers the key to changing manufacturing by driving efficiency, reducing waste, enhancing quality, enabling continuous process improvements, supporting new product development giving a clearer picture on business strategy, and more. It offers an exciting and highly promising sea change in manufacturing.
IIoT platforms have been touted by some as the replacement for Manufacturing Execution Systems (MES), yet the demand for MES is still growing. Research suggests manufacturers are failing with their IoT initiatives, supported by a report from Cisco that states that only 26% of companies surveyed considered their IoT Initiatives a success. The reasons for failure largely point to a lack of solutions focused on the distinct needs of manufacturing. A new approach is needed and those who are asking whether they should choose an IIoT Platform or MES are asking the wrong question. The question they should be asking is: “What do I need to succeed with IIoT and I4.0?” Asking this question gives space for the truth that existing applications and data sources are essential to the success of newer ones. MES is a proven application suite in manufacturing and logically, companies need both MES and IIoT platforms for manufacturing data management. In fact, the answer lies in a combination of technologies which include MES, IIoT, equipment integration and other elements for processing and analytics, ideally combined in a platform.
The data trap
Data is at the centre of smart manufacturing and one of the first keys to success is managing this data to gain insight into processes and procedures. In a manufacturing environment, data is plentiful, fast moving and exceptionally diverse. The possibilities of what can be done with this potential treasure trove of information is only really limited by the imagination – and this can be one of the first downfalls of an IoT project.
Massive volumes and different formats of manufacturing data can come from a wide array of equipment, devices, and systems. Taking a generic IoT platform and trying to analyze all this data is doomed to failure. Even the cost of storing the data in a data lake or on the cloud, can become hugely expensive.
Not all data needs to be analysed and the solution to the ‘data trap’ lies in having a clear business strategy and defined targets to identify relevant data. Data outside of the initial project targets, can be stored in its raw, unprocessed format with a system that can fetch this data when it is needed. If this is set up correctly, when a correlation between parameters and output results is identified, there is a waiting pool of historical data that can be readily used to feed Machine Learning (ML) algorithms to improve process outcomes.
As discussed, a pilot IoT project will likely need to handle huge volumes of data. When looking to scale up, these volumes can quickly become enormous and unmanageable. A data platform is therefore needed that can manage increasing volumes of data efficiently and inexpensively. A platform that utilizes a streaming data platform such as Apache Kafta, for example, can handle data in phases, splitting it down into ingestion, brokering (sending it where it needs to go), storage (where it can be used later in batch processing), transformation (calculations and analysis), and, finally, output. In this way, the data platform becomes a fault tolerant, central nervous system, acting across different applications and decoupling data streams from systems.
Unlocking the full value of IoT
A manufacturing IoT project has many different puzzle pieces. These include connecting varied devices, extracting relevant data, transmitting data to where it needs to go, standardizing protocols, visualizing data, analytics, and security. A generic IoT platform can do all of these but will require a heavy investment in the right resources and skills to create full value. Indeed, the amount of resources, work, and interdisciplinary collaboration needed to make the platform fit with a manufacturing environment, is one of the most likely reasons for a project to fail.
Instead of a generic IoT platform, if an IIoT platform specifically built for manufacturing is combined with MES, with a shared common data model, use cases that previously required heavy resourcing can become quick wins. This combined solution defines connectivity and integration with edge devices, other equipment, and business systems. The MES adds deep context with a data enrichment process and advanced analytics to make sense of the data collected. For sophisticated challenges, this platform will further provide the necessary tools, such as Apache Spark, a unified analytics engine with a complete sets of ML tools and algorithms, to create the exact solution required.
ML requires extremely detailed contextual information about data from diverse sources so that causal relationships can be identified. By combining MES, IoT, equipment integration, and data processing elements in a single platform, a holistic view of all relevant data is created and structured and unstructured datasets can be enriched to provide the context needed to learn from them. Data that has been contextualized, transformed, or enriched, is fed back into the ‘central nervous system’, so that it can be streamed where it needs to go in real-time or stored for later batch-processing analysis.
“Seeing the wood for the trees”
Generic, toolkit-style data platforms do not contain manufacturing use cases and may not provide the necessary detailed data to turn insights into actions. Platforms specifically designed for manufacturing, on the other hand, support more relevant use cases and make it easier to identify initiatives with fast return on investment (ROI). By employing both IoT and MES technology together, a complete end-to end process is supported out-of-the-box and both MES and IoT data can be used to identify hidden insights and high impact issues, take immediate action and close the loop.
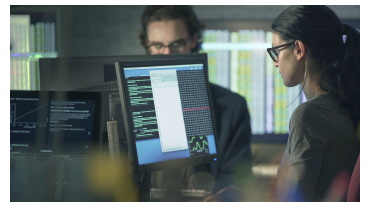
A combined IoT/MES platform enhances the capabilities of individual platform features. For example, the amalgamated data sources can provide more detailed reporting. More in-depth monitoring of processes can be provided to speed learning and deepen understanding of causes and effects. With full context and enrichment, synergies between data points can be more deeply explored to support decision making and identify areas of improvement.
Joining the dots
A successful, insightful data platform capable of driving continuous process improvements needs to bridge siloes of information. At the Operation Technology (OT) level, there could be thousands of different equipment types using different protocols or proprietary languages. Achieving data normalization is a key milestone in digital transformation.
An edge solution therefore needs to do more than just send data to an IoT platform. It needs to provide two-way edge-to-platform communication as well as being able to automate workflows, transform data, and communicate with other systems, including the MES. For this to be achieved, the edge platform should be agnostic to integration technology, be able to perform control-level logic, and have central management capability to enable deployment of communication drivers, automation workflows or master data as required.
Cybersecurity
Another common point of failure for IIoT projects is cybersecurity vulnerability. Data may need to be stored for long periods (particularly in regulated industries), be sensitive in nature, or have high competitive value. As the IoT collects exponentially increasing volumes of data and crosses between IT and OT, security is a particularly difficult challenge and poses a high risk to the business.
It makes more sense, therefore, to use an IoT data platform with multiple, proven security layers built in. The MES can be used to authenticate users and control security permissions. Using the industry standard HTTPS protocol, communication between clients and the application server can be secured. Object level security can further control which users are permitted to post events. Finally, APIs that use all the above security layers can be used to read data.
Taking a new approach
The issues detailed above mean that many IoT projects run over budget, take longer than planned, cost more, and deliver less value than anticipated, leading to a high likelihood of failure. The cost of storing and processing data with a generic IoT platform can be expensive and quickly escalate as the system grows.
In the first instance, identifying which processes to target and which challenges to solve is fundamental to a successful pilot IIoT project. If the wrong project is selected, the value of digital transformation will likely be lost to the wider enterprise. By selecting a project with a clear ROI, such as predictive maintenance, increasing yield, throughput efficiency, or time to market, and using a platform with out-of-the-box solutions for these, the chance of success increases dramatically. Manufacturers can achieve quick wins and then build upon their successes with new initiatives as more data become available over time.
By using a common data model inside one, unified platform, the new IoT Data Platform for manufacturing is a complete framework, incorporating MES, equipment integration, data standardization, security, and built-in manufacturing use-cases. It offers the functions needed in a manufacturing environment with the flexibility to add customised solutions for specific processing needs, provides seamless scalability and minimizes costs. More than anything, users will be selecting a platform that readily gives them the clarity they need and proven functions and tools to leverage the full benefits the IIoT has to offer.
Ultimately, discovering the hidden insights in data is the key to competitive advantage today and into the future. For this, you should not choose between an IIoT Data Platform and an MES but, for the best results and highest chance of success, fully leverage them both.
Contact Details and Archive...