The motor drive: A key player in predictive maintenance
07 May 2021
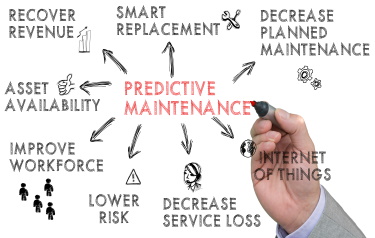
Shutterstock image
Predictive maintenance is fast becoming recognised as one of the more easily exploited applications of that popular but not always easily defined concept in industry – digitalisation. Also known as Industry 4.0, digitalisation remains a broad concept which can be difficult to justify in terms of investment. One aspect of digitalisation, however, stands out as worthy of swift and serious consideration: predictive maintenance.
Predictive maintenance can save millions of dollars of lost output by pre-empting production line downtime. In its predictive maintenance report, researchers at Interact Analysis have turned their focus on the ability of motor drives to perform predictive maintenance diagnostics not only on themselves, but also on the equipment they control, potentially saving millions in machinery downtime. This technology, whilst in its early days, is expected to be a key enabler of predictive maintenance initiatives as it opens up a new stream of data for both OEMs and end-users to tap into.
More than just a drive
Motor drives can be highly sophisticated pieces of equipment, capable of performing diagnostics on themselves, and giving signals to alert engineers when maintenance is necessary, thereby avoiding breakdowns and subsequent costly machinery downtime. Companies such as Siemens have recognised the potential of this predictive maintenance technology and offer it as a service to end-users through its digitalisation platform called Analyse MyDrives. However, drives can do more than diagnostics on themselves. For example, they can monitor the status of the motor they are controlling by measuring the voltage and current the motor requires to perform a task in real-time. This data is used to control torque and motor speed, but it can also be used to identify the imminent failure of a component in a motor. Drives vendors will argue that voltage and current measures give more sophisticated insights into motor failure than the standard monitoring of vibration. As OEMs and end-users are beginning to recognise the value of data housed in the smart devices driving their systems, some drives vendors are developing software for their products which are aimed at making the process of gathering, organising, and monitoring trends in this data easier. One of the earliest pioneers of this technology, and one of the strongest voices, has been Danfoss. The company has already brought this technology onboard with its VLT AutomationDrive and it is a great example of this trend in action.
Key considerations for drive vendors
Vendors offering drives incorporating predictive maintenance software need to ask themselves these questions:
• What data will be captured, and how?
• Where will the data be analysed?
• What is the most cost-effective option?
These questions have significance in terms of the capabilities of the drive from a predictive maintenance perspective. This is where vendors need be ready to respond to end-user needs when developing their products.
Regarding the kind of data captured, a lot depends on whether the drive acts as a sensor, collecting and analysing data, or as a gateway passing data on to an external network. A motor drive acting as a sensor will monitor voltage and current and flag up potential malfunctions in the motor equipment. It has been suggested that 70% of motor problems could be diagnosed by the drive in this way. However, for reasons of cost, not all drives have voltage and current sensors, so this is not an across-the-board solution. For a drive to act as a gateway, collecting data from third-party smart sensors, the drive vendor would need to decide which third-party protocols they would support, and what would be done with the data. Also, the drive would need to be fitted with additional hardware such as a networking IC.
If the drive could act both as a current and voltage sensor and a gateway to send more sophisticated data from smart sensors elsewhere to be analysed, it is most likely the vast majority of motor failure issues would be pre-empted. We believe this will be one solution offered by drive manufacturers, but it will take time, going beyond our forecast period, and it will not be useable technology on smaller, cheaper drives.
So, what is the best solution? Where should the data be analysed? And how can it be done most cost-effectively – on the drive or on the cloud? The problem with sensors is that they can produce a vast amount of data. If we only want to send key analytics of motor and drive performance to the network, all that information will have to be processed on the drive. The drive would need to be able to store this data, whilst simultaneously collecting new information, requiring both hardware and software modifications. In all likelihood, we expect drives as a sensor to be a premium feature within drives in the short term, and to gradually become the standard offering as demand for data from smart devices heightens.
Big players likely to be first in the queue for drive-based predictive maintenance technology
As a general rule, the bigger the motor, the greater the financial loss when it stands idle for repair. We believe the industries that will be first in the queue for motor drives offering predictive maintenance capabilities will be those using the largest and most expensive machinery. Additionally, process industries in which downtime could represent the loss of a batch being manufactured are expected to adopt predictive maintenance early. These industries are likely to include metals, oil and gas, water and waste-water, power, chemicals and pharmaceuticals, and various other sectors involving large industrial processes. As well as being the largest, they are also some of the swiftest growing sectors in the market. The potential for savings in these areas through predictive maintenance is huge. Automotive, another big player on the industrial landscape, has already started utilising predictive maintenance technologies. We anticipate these larger industries, often with multiple sites, will use a combination of edge and cloud computing for predictive maintenance analytics.
Smaller-scale industries may be slower to adopt predictive maintenance owing to cost issues, but we can expect these operations to increase their demand for drives that can diagnose issues on the spot, on the motors they are controlling.
Drive into a brave new world
Drive vendors offering equipment with smart sensor capability include ABB, Siemens and Danfoss. The ABB Ability Smart Sensor transfers data to a secure server via Bluetooth and can be used on traditional motors, pumps and bearing blocks. The Siemens SIMOTIQ IQ uses Bluetooth to communicate through gateways known as Connect 300 or Connect 400 to the cloud. Predictive maintenance enabled drive vendors include Rockwell Automation, Danfoss, and Schneider Electric. The Schneider AltivarProcess 630, used in a range of settings including pumping, lifting, aeration and compression operations can analyse data on the drive itself, or send it to an external network for processing.
Predictive maintenance in motor drives is a technology on the move. We expect to see this industry flourish as the cost benefits become more evident in an industrial environment where efficiency is key. Suppliers have already started working on the next generation of drives which incorporate predictive maintenance. These drives will not only identify an issue with a motor; they will also adjust its performance so it will keep running until an engineer can fix it. For industrial drives, it really is a brave new world out there.
To learn more about the predictive maintenance research, contact the senior analyst Blake Griffin directly on blake.griffin@interactanalysis.com
More information...
Contact Details and Archive...